Technology Areas/Product Groups
Planar wiring parts
FPC
For FPC, we are promoting product and technology development centered on deepening our focus on mobile and electronic devices, which have been our traditional main market, and on responding to the growing new needs of the automotive market.
Mobile and Electronic Devices
We are promoting development to support higher density and resolution as electronic information devices evolve, as well as higher frequency and higher speed transmissions that will accompany the increase in data transmission volumes such as 5G.
<High-definition technology>
We are currently developing high-definition circuit formation technology using the semi-additive method, aiming for practical mass production of L/S=10/10μm (see Photo 1).
<High frequency, high speed transmission FPC>
We are currently developing FPCs for internal wiring of devices that use low dielectric constant and low dielectric tangent materials compatible with 5G, and antenna substrates for the millimeter wave band (28GHz) (see Photo 2).
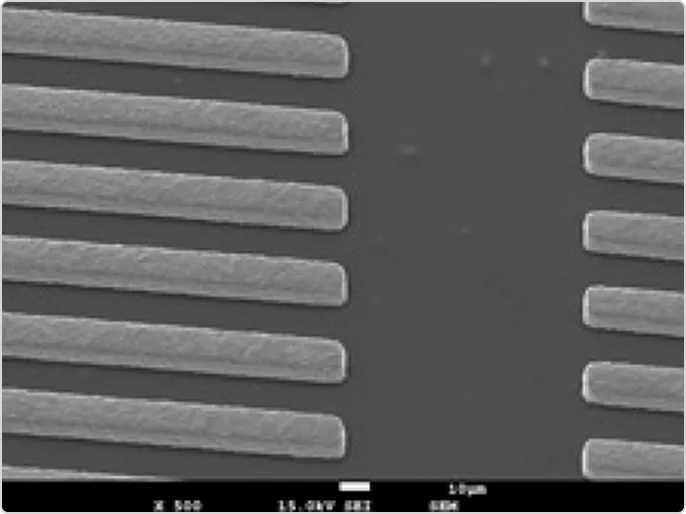
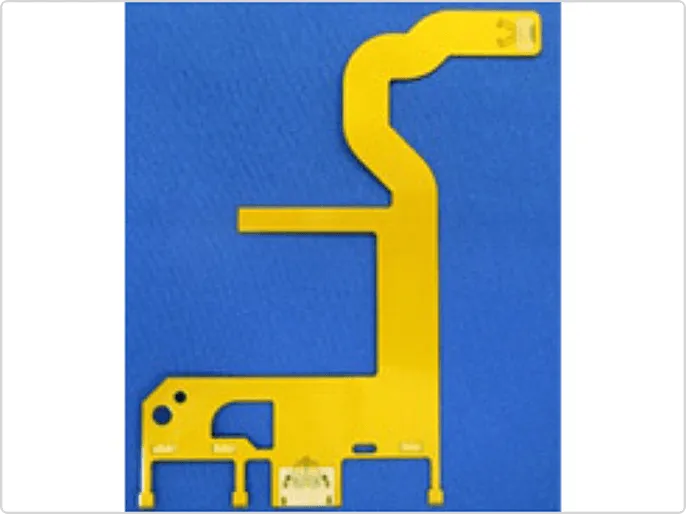
In-vehicle
As automobiles become more electronic, application of FPCs in in-vehicle applications is expanding, and we are promoting development to meet the needs for new functions and performance.
<High heat dissipation FPC>
For automotive LED lighting headlamp applications, which have high output, it is necessary to efficiently dissipate the heat generated by the LEDs, so we developed an FPC with high heat dissipation properties using materials and product structure with excellent heat dissipation properties (see Photo 3).
<Dissimilar metal joining technology>
For the purpose of application to high current applications, such as using the aluminum reinforcing plate used in FPCs as a current path, we have achieved a joint that suppresses the generation of intermetallic compounds when welding copper and aluminum using a unique welding method using our own fiber laser (see Photo 4 and Figure 1).
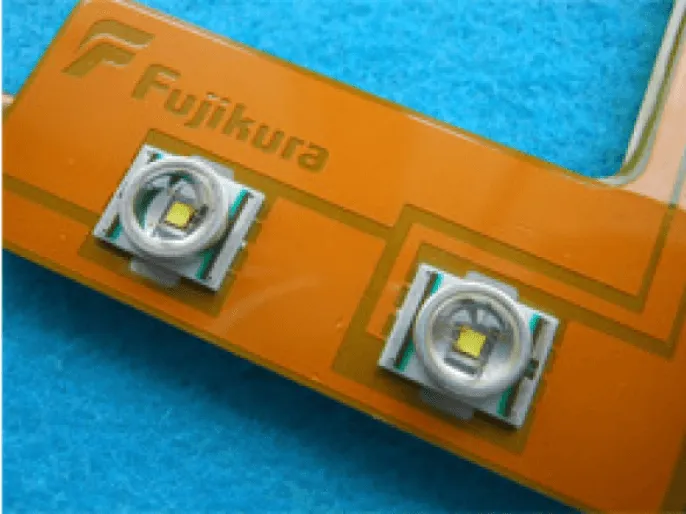
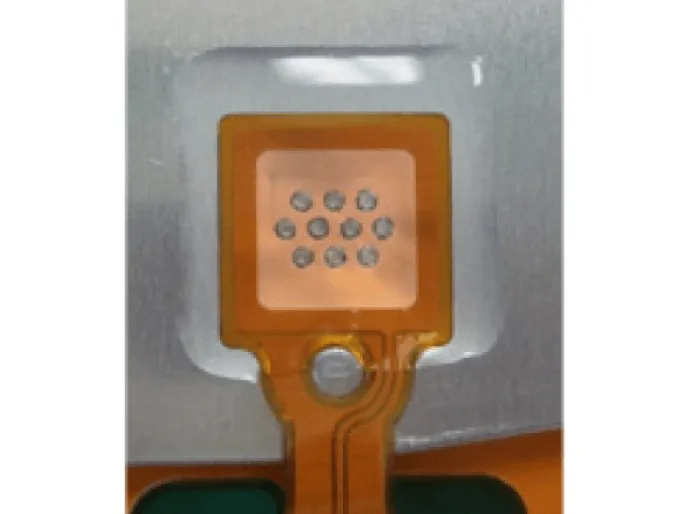
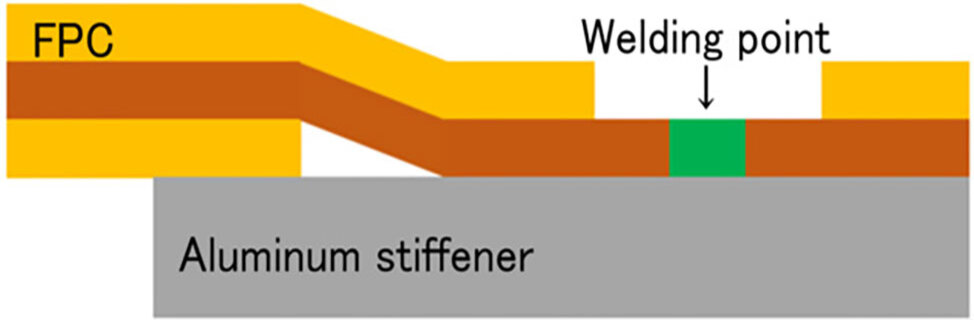
Solid wiring parts
We have developed a three-dimensional wiring component that integrates electronic circuits with a plastic case. This technology allows for three-dimensional molding without destroying flat printed circuits, making it possible to form electronic circuits on plastic components with uneven or curved surfaces.
It is possible to form multi-layer circuits on molded parts made of ABS or polycarbonate with a molding angle of 90° and a maximum unevenness of 10 mm.
This technology, which simultaneously creates three-dimensional circuits and processes resin for molding, not only dramatically improves the conventional assembly process, which required hand-processing of flexible circuit boards, but is also expected to improve product design and reduce the number of parts, making it application in home appliances and automotive products.
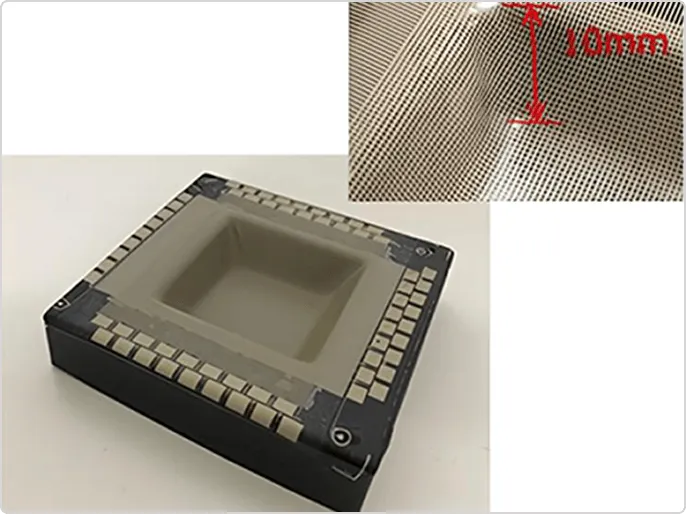
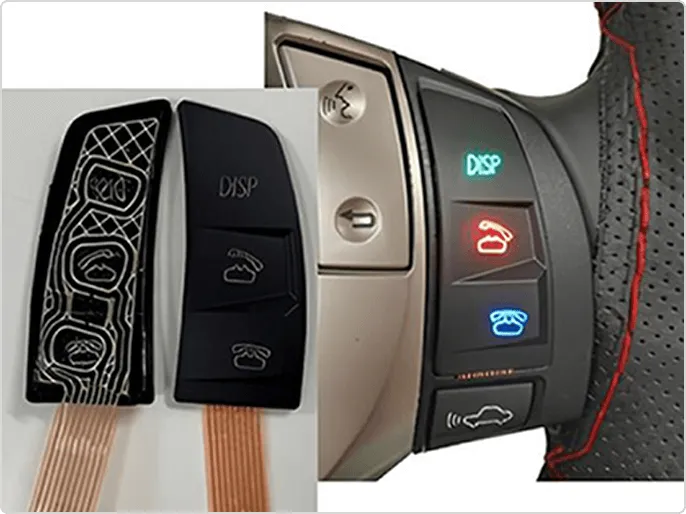
Ultra-fine coaxials
Micro coaxial cable assembly
In recent years, micro coaxial cables have been used for a variety of purposes, including mobile devices, wearable devices, and drones, and there is a need for connections with high bending and twisting characteristics in extremely limited spaces, as well as smaller diameters that are resistant to noise and transmit high-speed signals.
We are currently developing micro coaxial cables and assemblies for internal wiring in equipment that meet these needs through improvements to the internal cable structure, etc.
The photo on the right is an example of a highly flexible micro-coaxial cable. By changing the material and composition of the central conductor, we were able to achieve bending performance 10 times greater than that of conventional types. We can design and manufacturing cable structures to meet the desired bending performance.
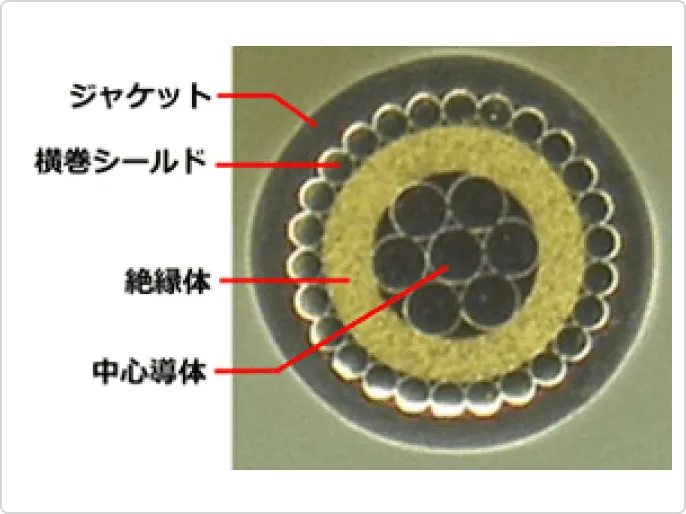
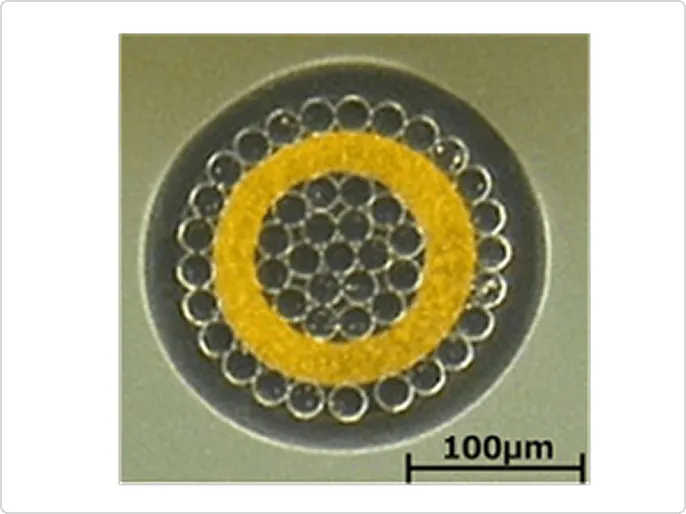
High Density Optical Cables
- 1) Increasing the number of cores laid in existing pipelines while using existing laying methods
- ② Shortening of splicing time by using SWR™ to splice ribbons together
- 3) Reduction in connection points by installing cables in a continuous manner from outdoors to inside the premises
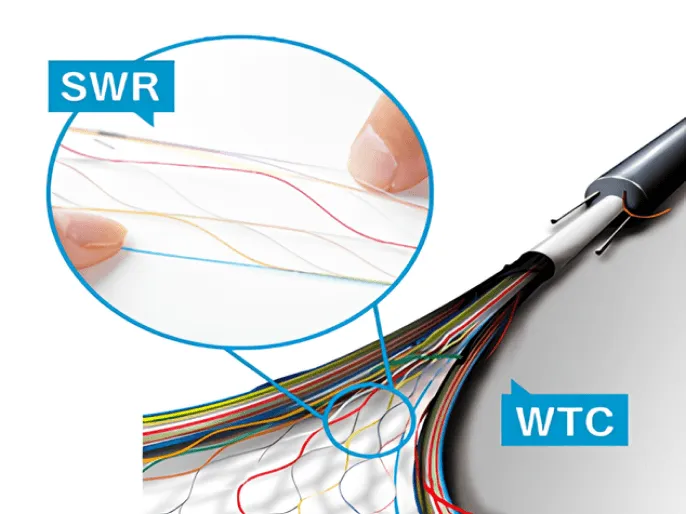
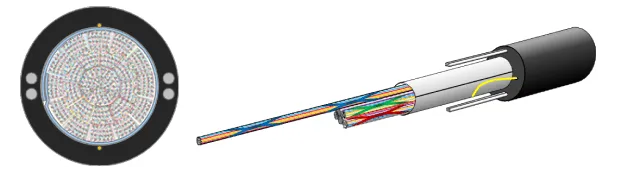
Ultra-thin high-density WTC®
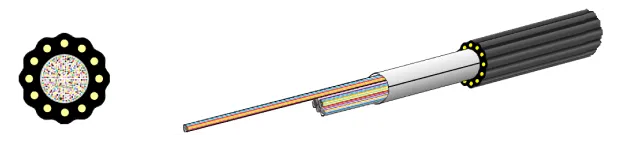
Air-blown WTC ® (AB-WTC™)
Electric Connectors
We have been developing, manufacturing, quality control (QC) and sales original connectors for approximately 60 years.
In recent years, there has been a strong demand for small and lightweight mobile devices such as smartphones, and connectors are also required to be "ultra-low profile," "ultra-compact," and "high mating operability."
We are developing connectors that incorporate small size, light weight and multi-function features to meet the demands of this market.
In order to meet further demands in the future, we will refine the following technologies and develop world-class ultra-miniature connectors.
Design Technology
- Structural analysis technology developed over many years to ensure contact reliability
- Flow analysis technology that allows resin to be filled even in thin walls (FTTH)
Production Engineering
- Press die manufacturing technology/press processing technology
- Resin molding die manufacturing technology/Thin-wall resin molding technology
- High-speed automatic inspection, assembly and packaging technology
- Gold-saving plating technology for ultra-small terminals
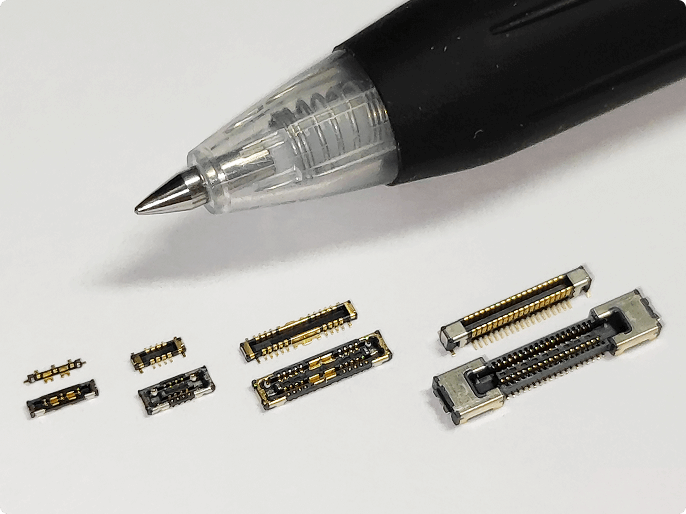
Board-to-board connector (FB3A series)
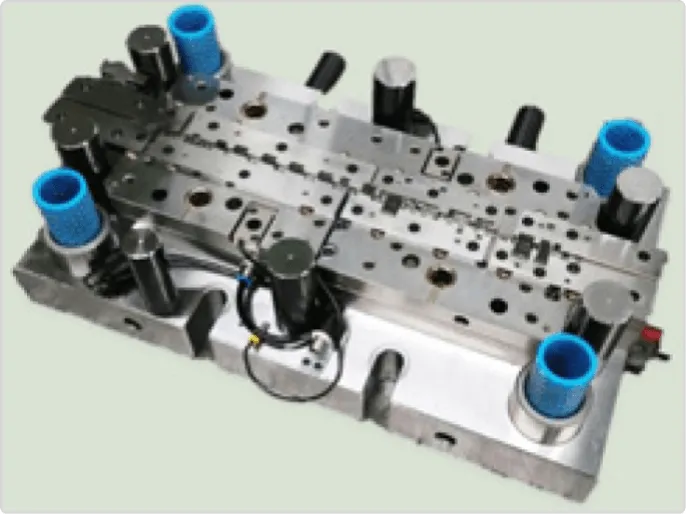
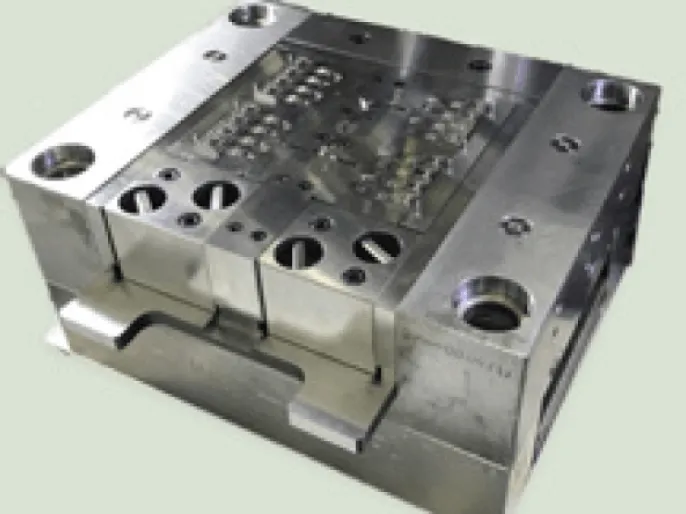
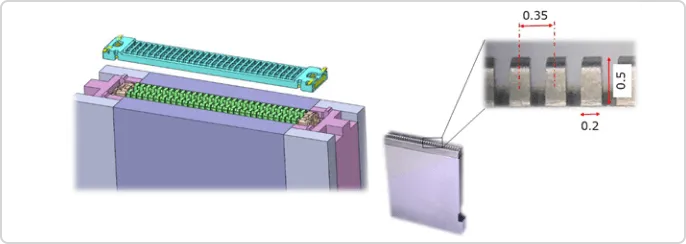
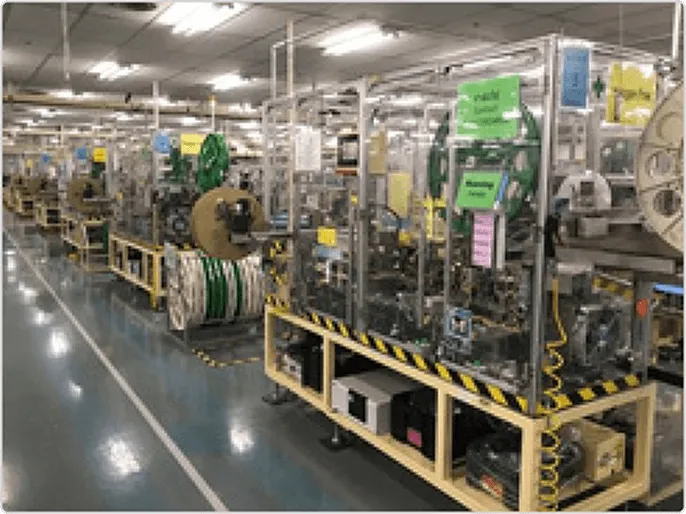
Wire harness
Wire harness, which have been likened to the "nerves and blood vessels of a car," are bundles of wires that act as "electrical pathways to ensure the normal operation of electronic units inside the car," connecting power sources and signals to every corner of the car.
As the number of electronic devices in vehicles increases year by year, Wire harness are also becoming more complex.
Fujikura utilizes the latest technology and the knowledge and experience it has accumulated over many years to provide a complete range Wire harness, from wiring materials and in-vehicle wiring systems to fuse boxes, connectors and terminals.
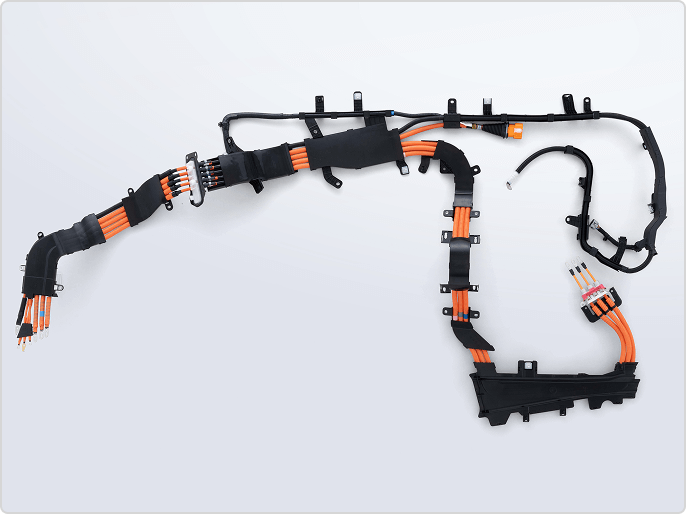
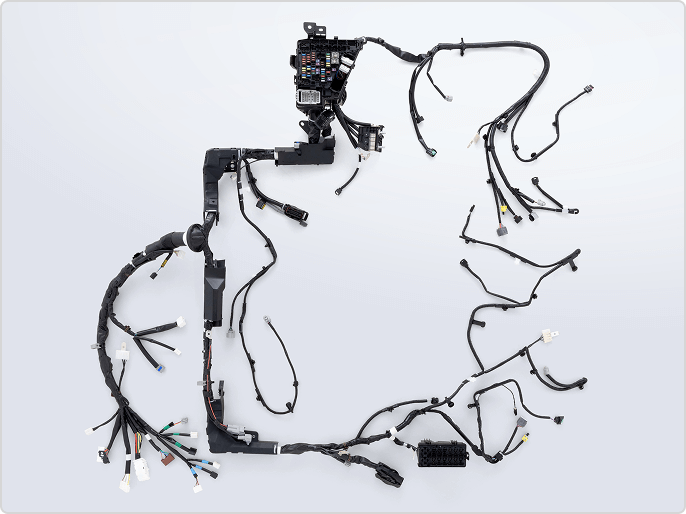
Heat Transport Devices
Power semiconductor cooling module
We are developing large-capacity heat pipes and vapor chambers to dissipate heat from power semiconductors that generate large amounts of heat. The vapor chamber is a flat heat pipe, and since the entire surface has the performance of a heat pipe, it has high heat dissipation performance. By improving the internal structure, we are promoting development to increase the maximum heat transport capacity and reduce thermal resistance.
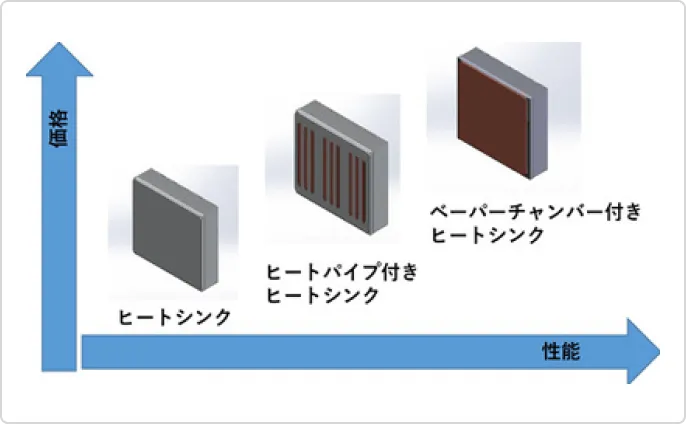
Cold plate for high performance computer
We have developed a liquid cooling unit called a cold plate, which uses a microchannel fin structure (fin thickness 0.15 to 0.4 mm) as a heat dissipation measure for high performance computers such as supercomputers and mainframes. Compared to air-cooling methods, cold plates require less space and have several times the cooling performance.
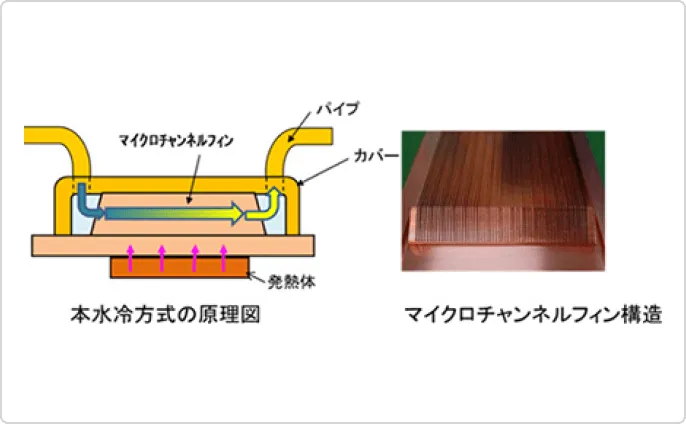