Technology Areas/Product Groups
Optical Connector
Optical connectors are products that precisely align the axes Optical Fiber and bring the end faces close together or into contact to achieve low-loss, highly reliable repeatable connections. Optical connectors are application for single-core fiber connections and multi-core bulk connections (Fig. 1), and there are multiple connection methods for each. Fujikura has core technologies in each connection method and provides a variety of solutions to meet customer applications. PC connections are a method in which the end faces Optical Fiber are physically contacted with each other, and Fujikura has developed low-loss, multi-core optical connectors using high-precision polishing technology and precision resin molding technology. In addition to PC connections, we also provide field-assembled optical connector solutions (Fig. 2) that combine refractive index matching materials and connections using Fusion Splicer. In addition, in recent years, the increase in data traffic in hyperscale data center (HSDCs) has led to increased density in optical connectors and optical wiring solutions. As a solution to this problem, Fujikura is expanding its MMC ferrule connectors (Fig. 3), which are key components for small and high-density connections, and wiring solutions into these new fields. In addition, we are currently developing products compatible with 80um clad fibers to achieve even smaller and higher density. We are also working on the development of an MCF-MPO connector (Figure 4), which is a multi-core optical connector assembled from multi-core fibers that have multiple cores, which are the paths for multiple signals, in a single fiber, enabling even higher density.
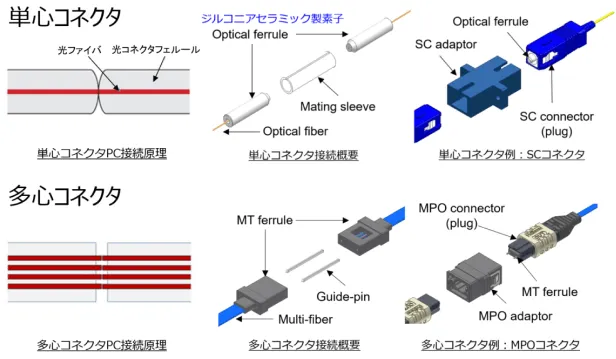
Figure 1: Single-fiber and multi-fiber connectors
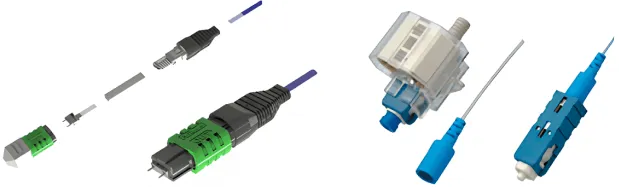
Figure 2: Examples of field-assembled connectors (Left: fusion-type MPO connector, Right: refractive index-matched single-fiber connector)
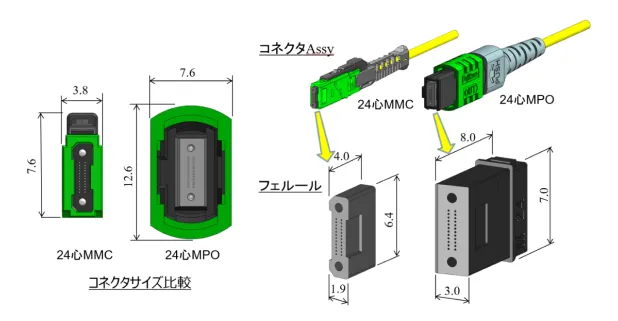
Figure 3: MMC vs MPO connector comparison
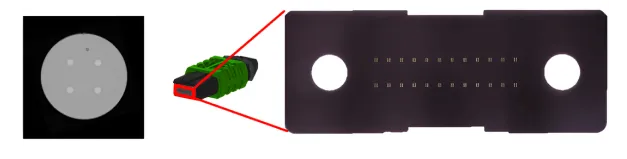
Figure 4: Multicore fiber (left) and MCF-MPO connector (right)
Fusion Splicer
We are working on the research and development of equipment for removing the coating of Optical Fiber, cutting, and fusion splicing. The core position of Optical Fiber is measured with high precision, two Optical Fiber are aligned at the submicron level using a precision axis alignment mechanism, and fusion splicing is performed using quasi-corona discharge or CO2 laser. Fusion splicers using quasi-corona discharge with tungsten electrodes can be made compact and are mainly used to connect Optical Fiber for communication. On the other hand, Fusion Splicer using CO2 lasers do not cause tungsten to adhere to Optical Fiber and are mainly used to process special Optical Fiber. The characteristics of CO2 lasers are utilized not only for connecting, but also for processing tip lenses and manufacturing optical couplers. This equipment, which makes full use of mechatronics technology, has established a position as the world's top share.
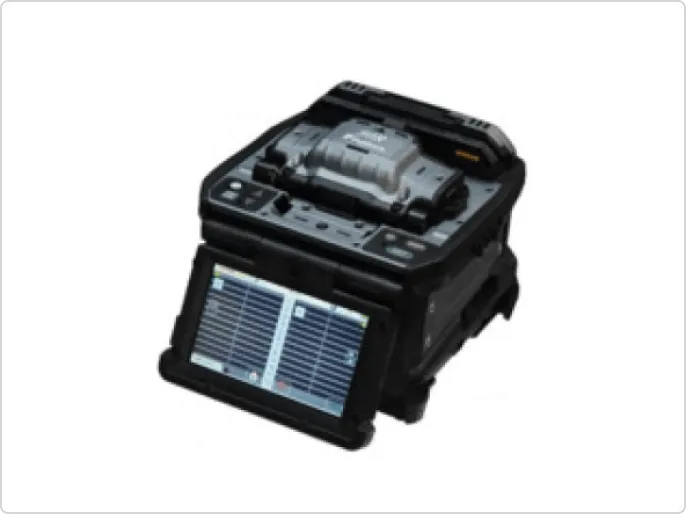
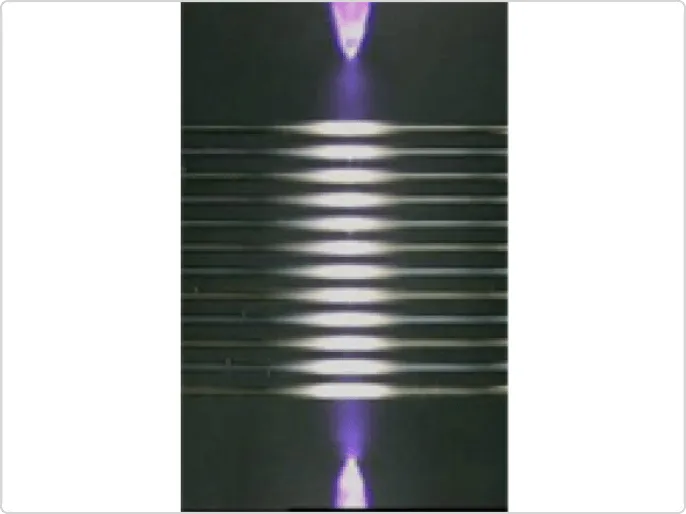
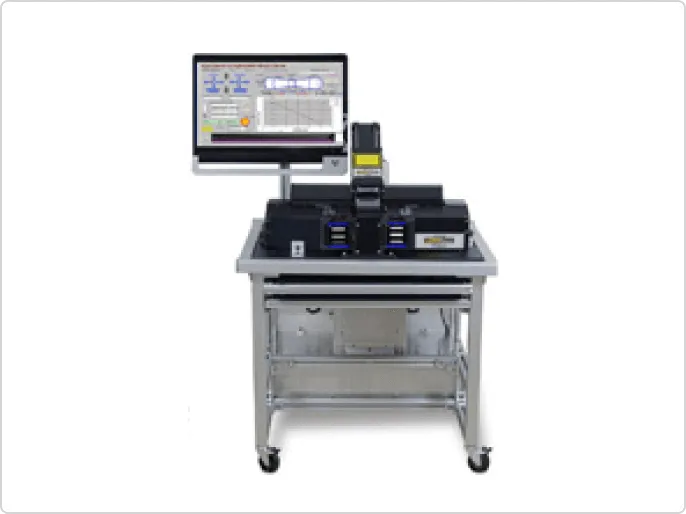
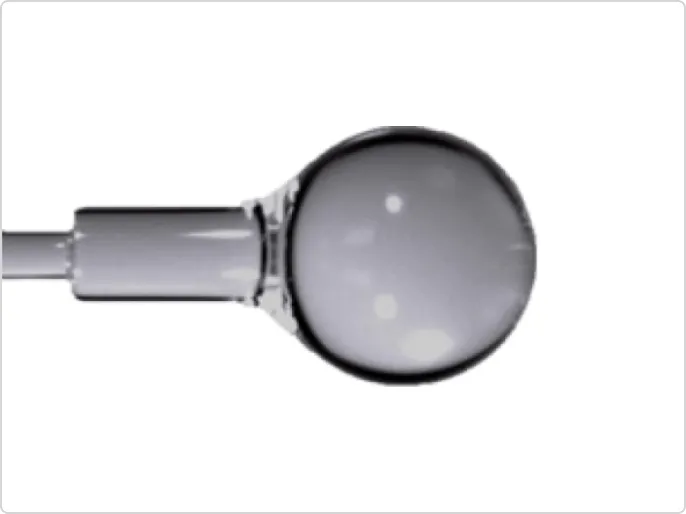
High Density Optical Cables
- 1) Increasing the number of cores laid in existing pipelines while using existing laying methods
- ② Shortening of splicing time by using SWR™ to splice ribbons together
- 3) Reduction in connection points by installing cables in a continuous manner from outdoors to inside the premises
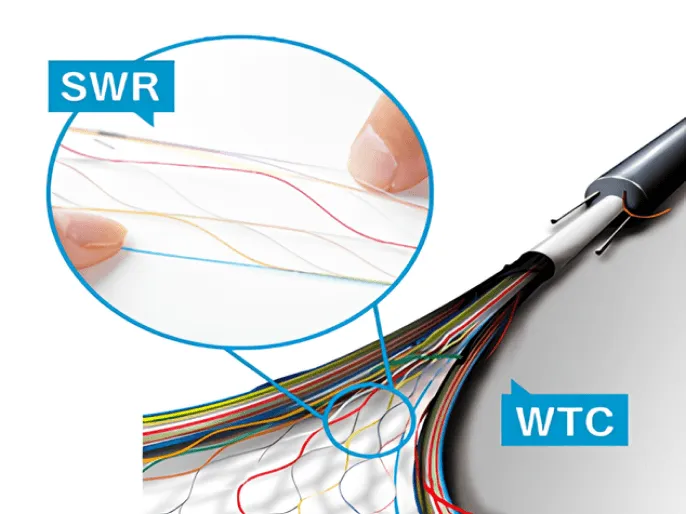
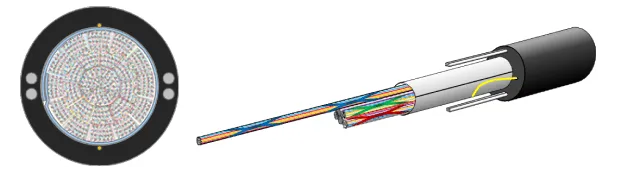
Ultra-thin high-density WTC®
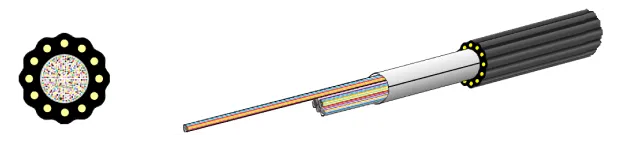
Air-blown WTC ® (AB-WTC™)
Electric Connectors
We have been developing, manufacturing, quality control (QC) and sales original connectors for approximately 60 years.
In recent years, there has been a strong demand for small and lightweight mobile devices such as smartphones, and connectors are also required to be "ultra-low profile," "ultra-compact," and "high mating operability."
We are developing connectors that incorporate small size, light weight and multi-function features to meet the demands of this market.
In order to meet future demands, we will refine the following technologies and develop world-class ultra-miniature connectors.
Design Technology
- Structural analysis technology developed over many years to ensure contact reliability
- Flow analysis technology that allows resin to be filled even in thin walls (FTTH)
Production Engineering
- Press die manufacturing technology/press processing technology
- Resin molding die manufacturing technology/Thin-wall resin molding technology
- High-speed automatic inspection, assembly and packaging technology
- Gold-saving plating technology for ultra-small terminals
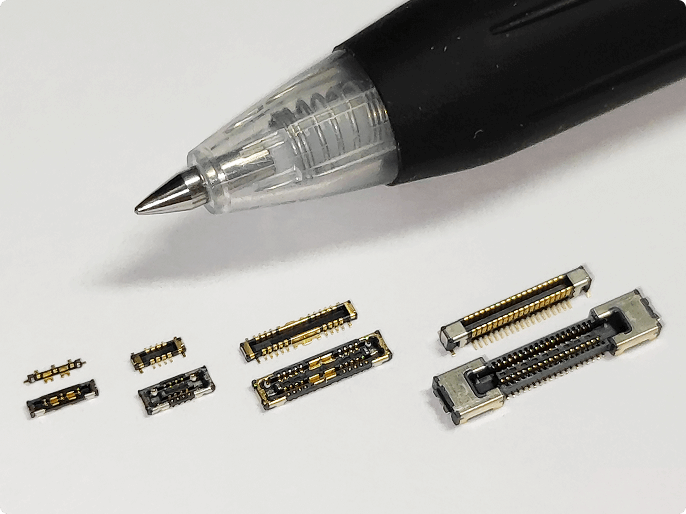
Board-to-board connector (FB3A series)
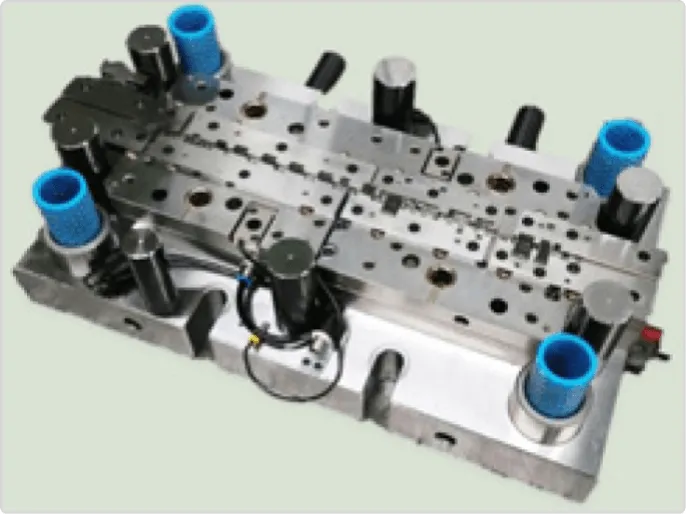
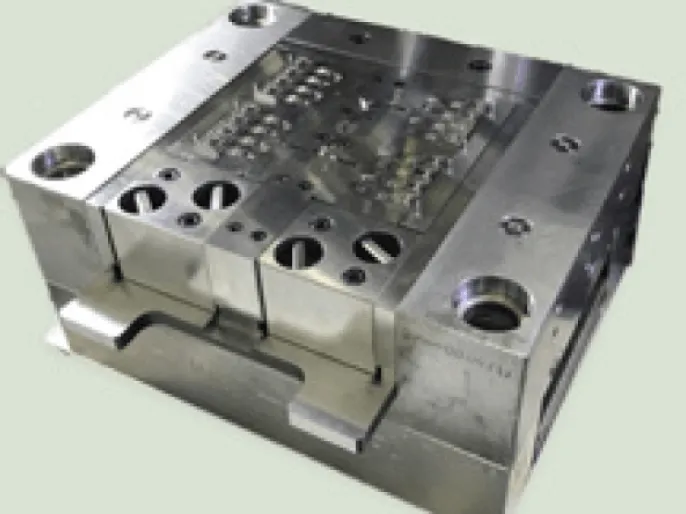
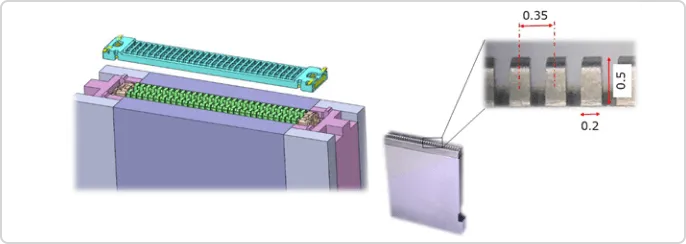
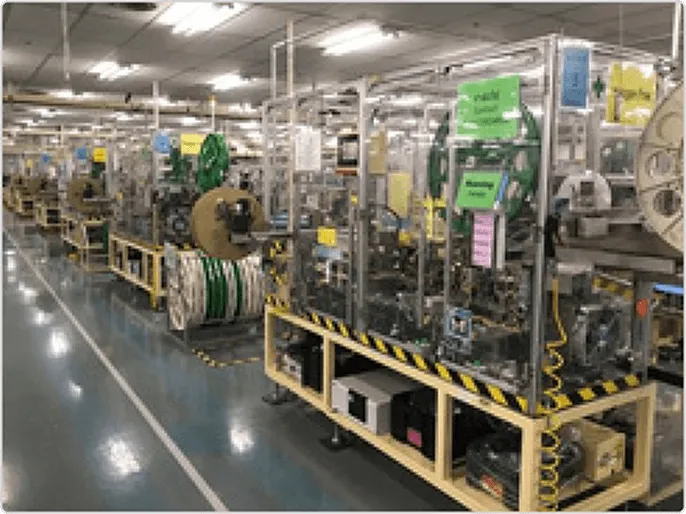
Wire harness
Wire harness, which have been likened to the "nerves and blood vessels of a car," are bundles of wires that act as "electrical pathways to ensure the normal operation of electronic units inside the car," connecting power sources and signals to every corner of the car.
As the number of electronic devices in vehicles increases year by year, Wire harness are also becoming more complex.
Fujikura utilizes the latest technology and the knowledge and experience it has accumulated over many years to provide a complete range Wire harness, from wiring materials and in-vehicle wiring systems to fuse boxes, connectors and terminals.
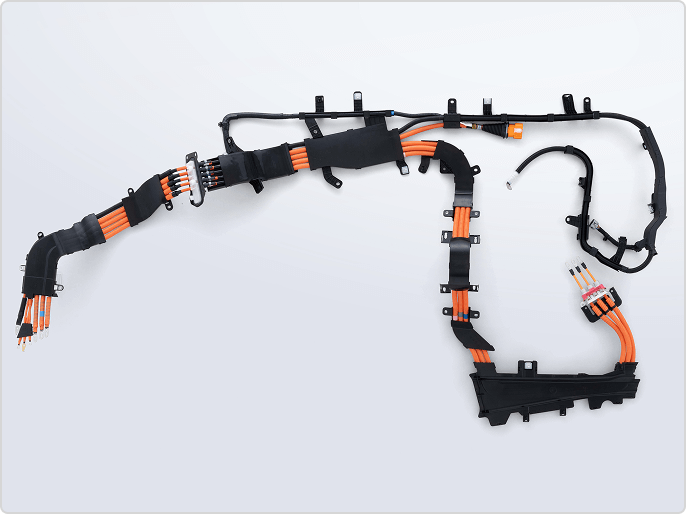
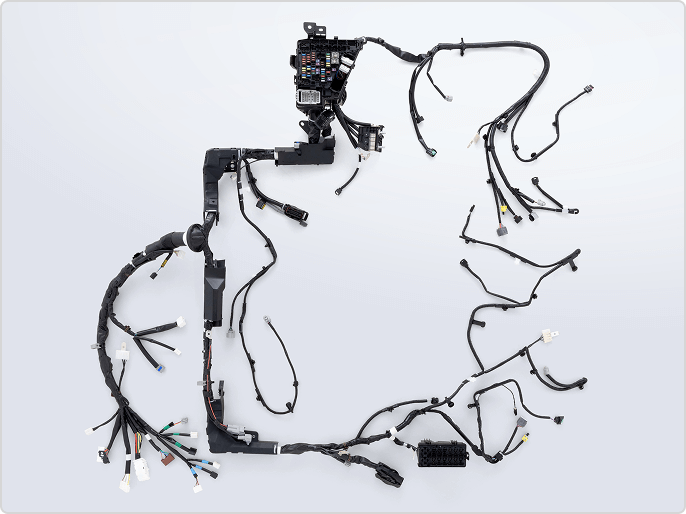
High Current Connection
One of the challenges in the spread of electric vehicles (EVs) is shortening the charging time. To shorten the charging time, it is necessary to increase the charging current, but this causes the problem of increased heat generation inside the charging cable connector. The amount of heat generated can be reduced by increasing the size of the cable conductor, but this increases the weight and size of the cable, which reduces operability during charging. Therefore, in order to increase the charging current without increasing the size of the cable conductor, we have developed a liquid-cooled cable connector that application liquid cooling technology that efficiently dissipates heat by circulating a liquid refrigerant inside the cable connector. This has achieved a rated charging current that is more than three times higher than conventional models, without compromising operability in terms of weight and size.
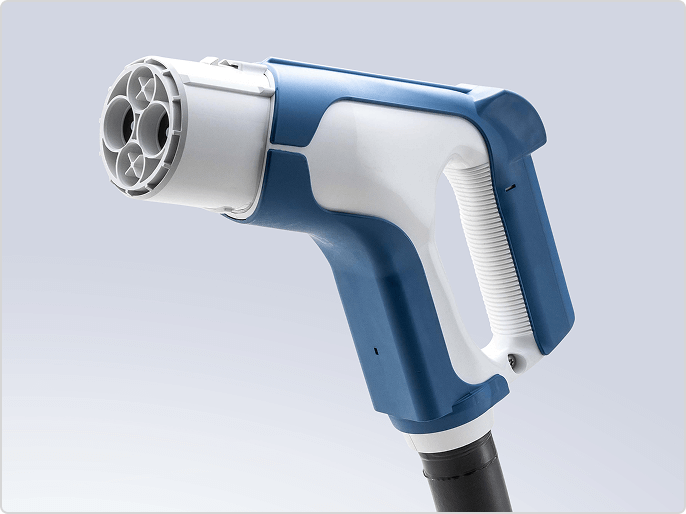