Company Data
Management Philosophy
Basic Concept
In order to prevent recurrence of quality inappropriate cases, we have formulated and are working to realize "the ideal state of quality assurance (QA)" regarding the independence of quality assurance (QA) and the electronicization of quality data. In addition, in the unlikely event that a quality inappropriate act does occur, we will establish a system for escalating information, reporting to customer, and ensuring the implementation of corrective measures, and strive to prevent recurrence.
Fujikura Quality policy (revised in April 2019)
- 1.To provide customers with products and services that are of the highest quality by pursuing a management philosophy based on Quality.
- 2To ensure that all employees continuously engage in proper conduct related to quality control by complying with all laws, regulations and contracts with customers, based on a strong awareness of the importance of quality compliance.
- 3To always encourage communication within the workplace to foster an open corporate culture, and promptly report to superiors when problems of quality compliance are recognized.
Quality Assurance System
The Fujikura Group are developing company-wide TQM activities based on quality management systems (QMS) such as ISO 9001 to meet the trust and expectations of our customers.
Fujikura holds regular company-wide quality strategy meetings and quality assurance (QA) managers' meetings hosted by the director in charge of the Corporate Quality Management Unit to determine quality policy, quality targets, and quality KPIs, and to deliberate and make decisions on quality-related issues. In addition, internal quality assurance audits are conducted on each business division and group companies to maintain and improve quality based on each division's quality performance and other information.
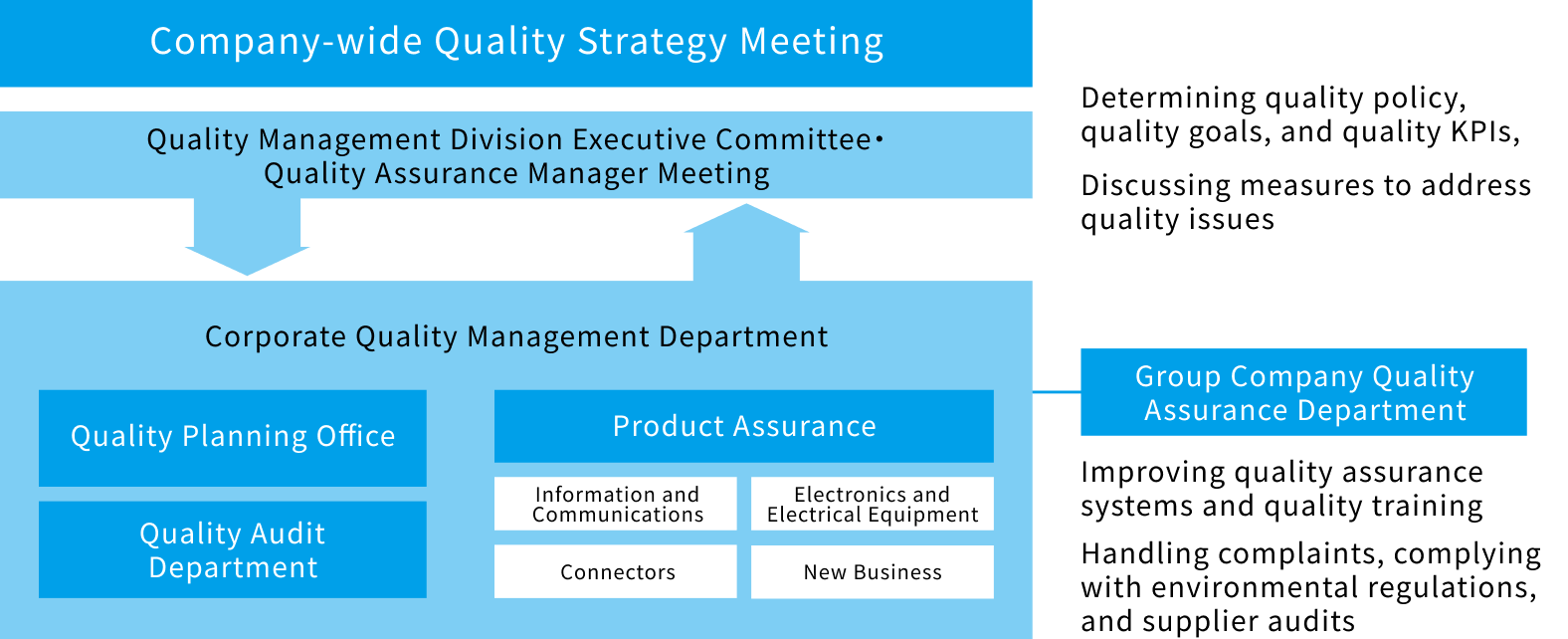
Quality-Related Complaints
Quality complaints are the last thing customers want, and Fujikura is continually working to reduce them as a top priority. Fujikura Group carries out most of manufacturing at group companies both in Japan and overseas, and in order to prevent the recurrence of quality complaints, we work with group companies to identify the causes and implement measures. Since fiscal 2013, we have introduced quality-related KPIs and are working to understand and improve the quality of the entire Fujikura Group under unified standards.
In the event of a serious complaint, we promptly report it to the Corporate Quality Management unit Executive and management layer, and take measures to prevent recurrence, such as having a special team investigate the cause. Fujikura Group will continue to promote its quality assurance (QA) activities with the goal of "zero serious complaints."
Measures for Product Safety
Quality-Related Complaints are the last things customers want to have, so Fujikura continues to make efforts to minimize any complaints. Most manufacturing is done at domestic and international Fujikura group companies, and to stop re-occurrence of Quality-Related complaints, our group companies cooperate to research reasons for claims and implement responses.
Corporate Quality Management Unit operates as an independent organization separate from the business divisions. In order to enhance the independence of quality assurance activities, we are diligently implementing a clear division of responsibilities, including group companies, and advancing the digitization of systems.
The Fujikura Group Basic Policy on Product Safety
-
1Compliance with law
- ●Grasp the latest information on laws and regulations regarding product safety and comply with them.
- ●Establish or revise in-house regulations according to these laws and regulations and inform the employees of the change.
-
2.Ensuring of product safety
- ●In order to provide customers with safe products, we utilize various reliability methods and take every possible measure to ensure safety in our designs.
- ●To ensure proper use of our products, necessary instructions and warnings will be displayed on the product and in the instruction manuals.
-
3.Response to product accidents
- ●In the event of a product accident, we will quickly gather information and provide it appropriately.
- ●Depending on the impact of the product accident, measures such as recall or repairs will be taken.
-
4.Continuous Improvement
- ●Each business entity will implement the voluntary action plan it has formulated and work toward continuous improvement.
- ●Through this continuous improvement, we will establish a corporate culture that ensures product safety so that customers can use our products with confidence.
Corporate Quality Management Unit operates as an independent organization separate from the business divisions. In order to enhance the independence of quality assurance activities, we are diligently implementing a clear division of responsibilities, including group companies, and advancing the digitization of systems.
Progress of Action Plan for Cases of Unsuitable Quality
Based on the measures to prevent recurrence announced on April 25, 2019, the Fujikura Group is working on "governance reform," "adequate understanding of manufacturing process capabilities and inspection capabilities and confirmation of customer required specifications," and "improving awareness of quality compliance."
We started work on all preventative measures during FY2019,and valuated the effectiveness of the measures we evaluated the effectiveness of the measures every year. We believe that continuing and improving measures to prevent recurrence across the Fujikura Group is important in preventing any further quality improprieties, and will therefore strive to improve governance and strengthen our quality assurance (QA) system.
Please click here for the presentation materials regarding this matter.
-
Measures to prevent recurrence of inappropriate quality control (QC) cases involving some of our products and progress in confirming the safety of the inappropriate products (FY2020)
-
Progress of safety checks and preventative measures regarding quality control (QC) issues in some of our products (FY2019)
-
Progress of Safety Confirmation and Measures to Prevent Recurrence Regarding the Company's Inappropriate Activities
-
Regarding lifting of suspension of ISO9001 certification
-
Regarding lifting of suspension of ISO9001 certification
-
Suspension of ISO9001 certification
-
Regarding the lifting of the "Temporary Suspension of Use of JIS Marks, etc."
-
Regarding lifting of suspension of ISO9001 certification
-
Report on the results of an investigation into improper quality control (QC) issues regarding some of our products
-
Suspension of ISO9001 certification
-
Regarding lifting of suspension of ISO9001 certification
-
Regarding lifting of suspension of ISO9001 certification
-
Suspension of ISO9001 certification
-
Regarding "Temporary Suspension of Use of the JIS Mark, etc."
-
Suspension of ISO9001 certification
-
Apology and Notice Regarding Improper quality control (QC) of Some of Our Products