Technology Areas/Product Groups
High-Temperature Superconducting Wire
High-temperature superconducting technology is expected to contribute to the realization of a carbon-neutral society in a wide range of fields, including energy, industry and transportation, and medicine and analysis. In particular, in the energy field, expectations have been rising in recent years for nuclear fusion power generation to be one of the future power generation methods as a next-generation energy source.
Compared to conventional power generation, nuclear fusion power generation does not emit carbon dioxide, and the resources are abundant in seawater. It is also considered to be superior in terms of safety as it does not go into thermal runaway, and is expected to be a technology that will fundamentally solve our energy and environmental problems.
In recent years, mainly in Europe and the United States, there has been a movement to accelerate the practical application of nuclear fusion power generation by making the superconducting magnets required for nuclear fusion power generation smaller than conventional ones through the adoption of rare earth high temperature superconducting wire. Our company continues to conduct world-class research and development of high temperature superconductivity, and provides high performance, uniform rare earth high temperature superconducting wire both domestically and internationally, earning high praise from users.
In addition to contributing to the development of nuclear fusion power generation, Sumitomo Electric will also contribute to the realization of a carbon-neutral society through its contributions to a variety of next-generation superconducting equipment, including electric aircraft and analytical instruments.
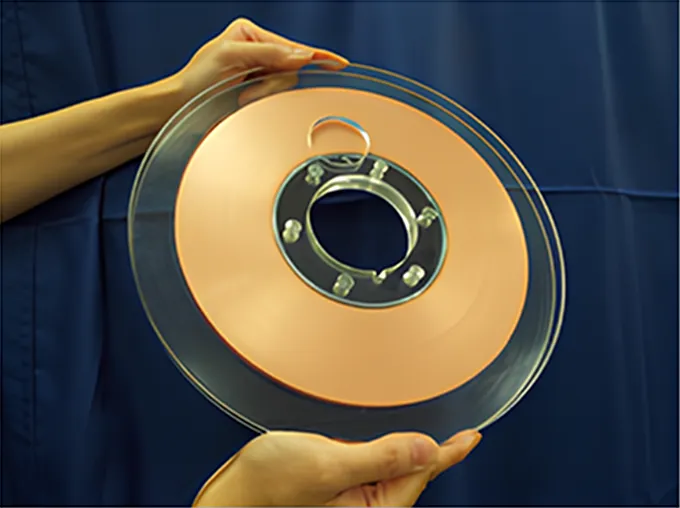
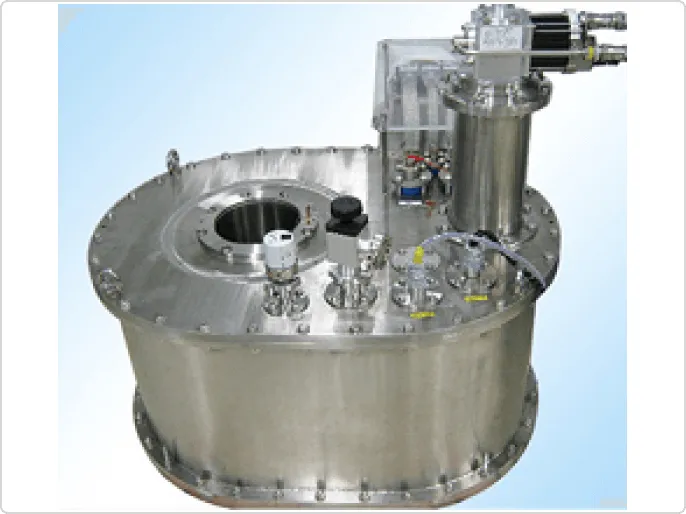
Fiber Laser
Among Fujikura products, high-power continuous wave multimode fiber lasers (Figure 1) are used for metal cutting and welding, while continuous wave single mode fiber lasers with excellent beam quality are used for joining different materials and cutting carbon fiber reinforced plastics (CFRP), etc. In addition, Q-switched pulsed fiber lasers are used for marking and metal processing, and MOPA pulsed fiber lasers (Figure 2) are used for micromachining of various materials.
As described above, fiber lasers are used in a wide range of processing fields, and their applications are expanding to include biotechnology, medicine, battery and semiconductor manufacturing. In order to keep up with these market demands, we continue to develop Fujikura proprietary elemental technologies that make up fiber lasers, such as high-power laser diodes, rare earth doping, special Optical Fiber, and fiber-type optical components, to realize new processing methods.
Recently, we have developed and are working to commercialize a wide range of technologies, including high-speed cutting of thick metal plates using a 20kW ultra-high-power continuous wave multi-fiber laser (Figure 3), beam profile variable technology that improves processing quality by controlling the laser beam shape (Figure 4), and wavelength conversion technology that improves processing speed by adjusting the wavelength of light to one that easily deteriorates the processing material.
Another promising future application for fiber lasers is wireless energy transmission using laser light. This is called a Space Solar Power System (SSPS), in which solar energy in space is transmitted to the ground using laser light, and the laser light is then converted into electricity on the ground. Research and development into this system is being carried out at many research institutes.
We will continue to research and develop fiber laser products and technologies to meet our customers' needs, not only enabling a wide variety of processing with high performance and high quality, but also contributing to society by reducing the environmental burden with high efficiency and energy saving.
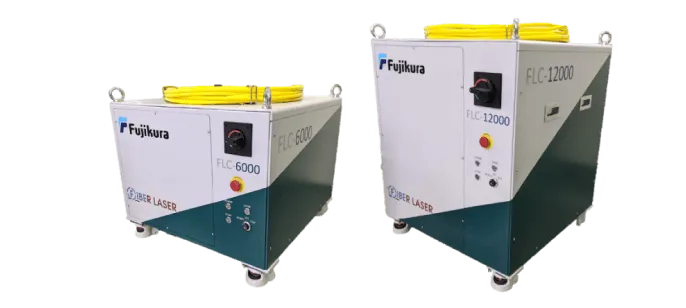
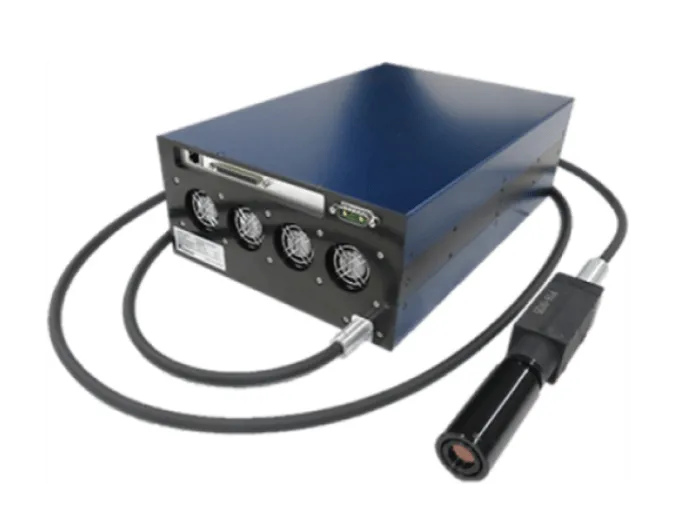
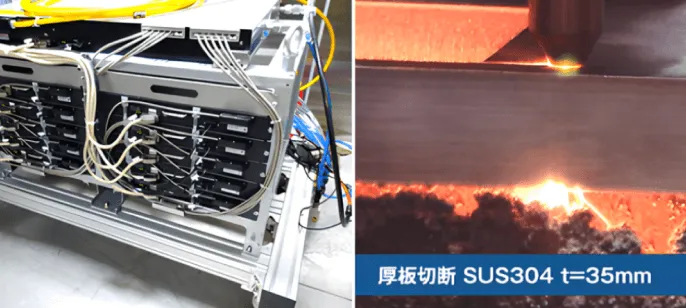
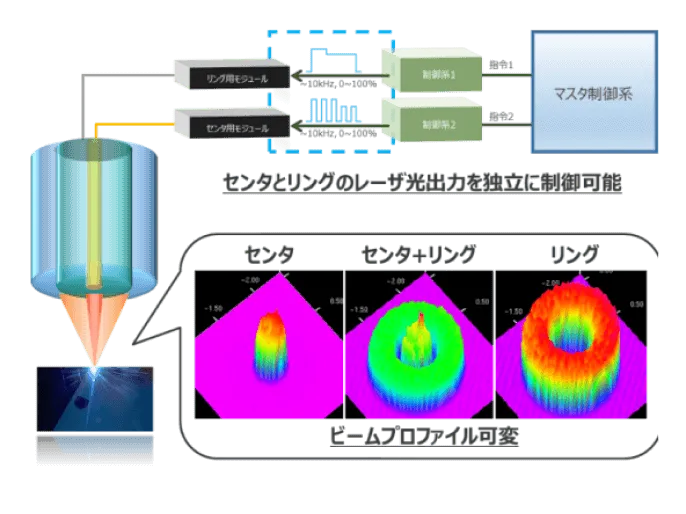
Conductor/Insulator
The conductor and insulating material technologies that have been cultivated over a long history of product development related to energy and information transmission have been a strong driving force behind Monodukuri of Fujikura Group. In recent years, for Wire harness conductors that contribute to weight reduction in automobiles, we have developed an aluminum alloy conductor that combines high strength, high conductivity, and high ductility by controlling the metal organization through consistent development from alloy composition to processing.
As a covering material for electric wires and cables, we aim to reduce the weight of the resin that constitutes it and reduce the energy consumption when installed in automobiles, thereby contributing to the SDGs of our products. In addition, we have provided safety and security to our customers by making flammable resin materials flame-retardant and using materials that are friendly to the human body and the environment. Going forward, we will continue to support the products and Monodukuri of Fujikura Group through our core material technologies.
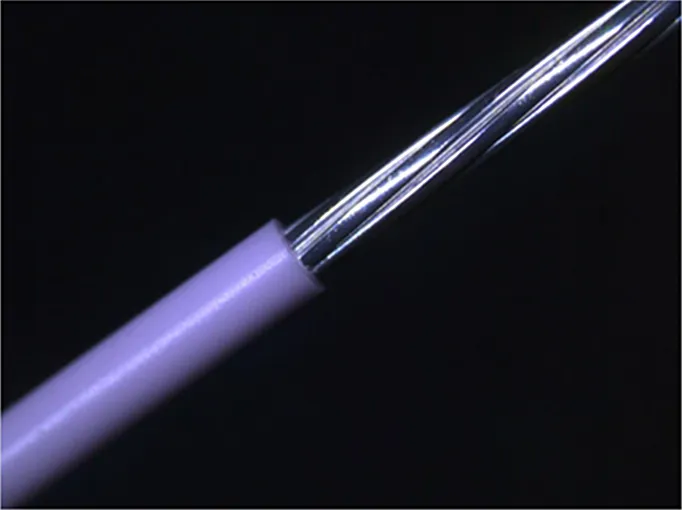
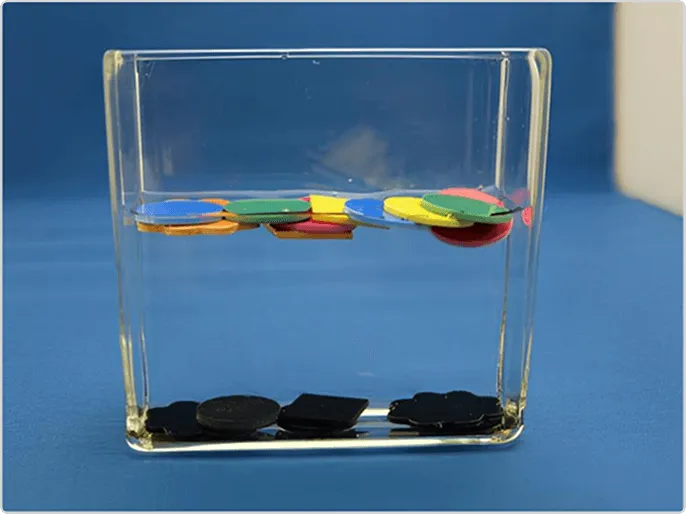
Heat Transport Devices
Power semiconductor cooling module
We are developing large-capacity heat pipes and vapor chambers to dissipate heat from power semiconductors that generate large amounts of heat. The vapor chamber is a flat heat pipe, and since the entire surface has the performance of a heat pipe, it has high heat dissipation performance. By improving the internal structure, we are promoting development to increase the maximum heat transport capacity and reduce thermal resistance.
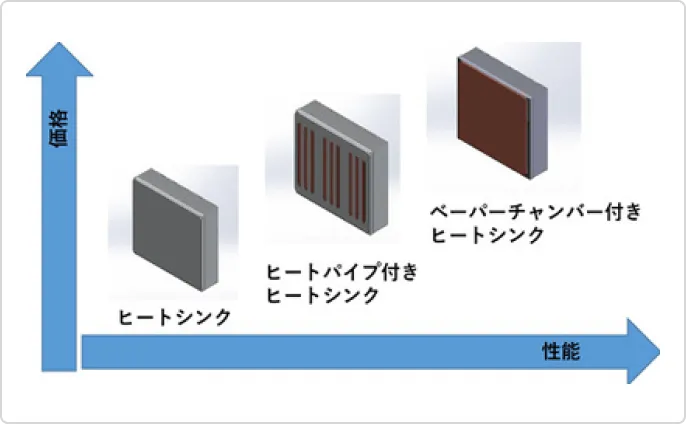
Cold plate for high performance computer
We have developed a liquid cooling unit called a cold plate, which uses a microchannel fin structure (fin thickness 0.15 to 0.4 mm) as a heat dissipation measure for high performance computers such as supercomputers and mainframes. Compared to air-cooling methods, cold plates require less space and have several times the cooling performance.
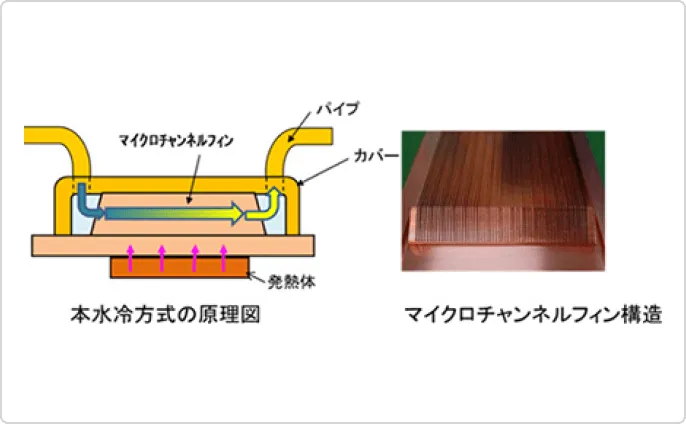
Wire harness
Wire harness, which have been likened to the "nerves and blood vessels of a car," are bundles of wires that act as "electrical pathways to ensure the normal operation of electronic units inside the car," connecting power sources and signals to every corner of the car.
As the number of electronic devices in vehicles increases year by year, Wire harness are also becoming more complex.
Fujikura utilizes the latest technology and the knowledge and experience it has accumulated over many years to provide a complete range Wire harness, from wiring materials and in-vehicle wiring systems to fuse boxes, connectors and terminals.
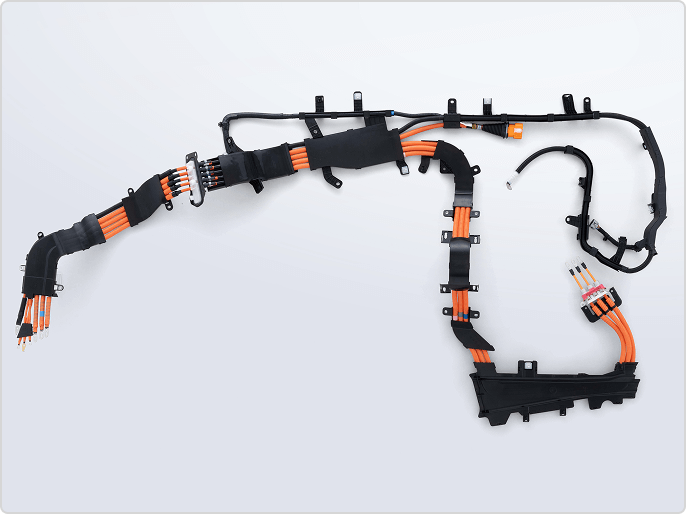
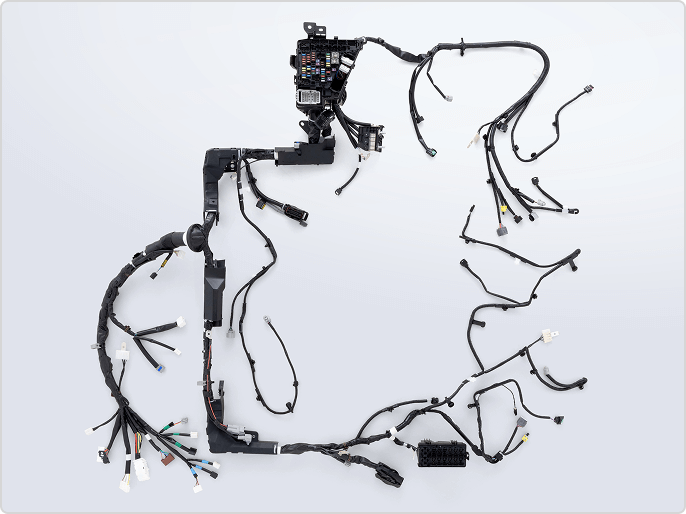
High Current Connection
One of the challenges in the spread of electric vehicles (EVs) is shortening the charging time. To shorten the charging time, it is necessary to increase the charging current, but this causes the problem of increased heat generation inside the charging cable connector. The amount of heat generated can be reduced by increasing the size of the cable conductor, but this increases the weight and size of the cable, which reduces operability during charging. Therefore, in order to increase the charging current without increasing the size of the cable conductor, we have developed a liquid-cooled cable connector that application liquid cooling technology that efficiently dissipates heat by circulating a liquid refrigerant inside the cable connector. This has achieved a rated charging current that is more than three times higher than conventional models, without compromising operability in terms of weight and size.
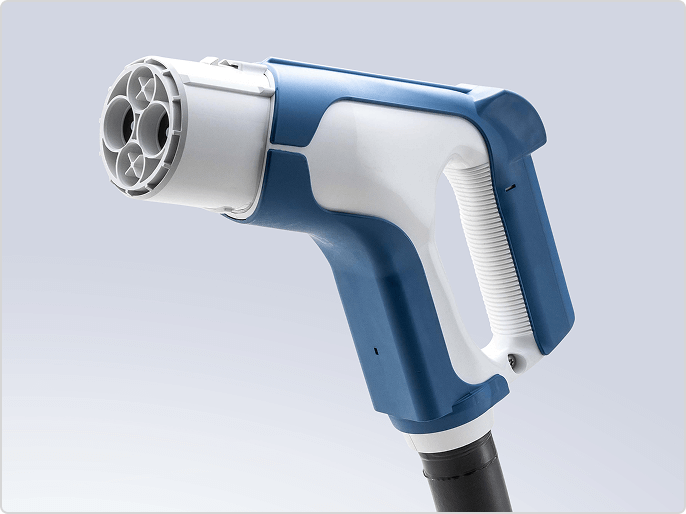