Technology Areas/Product Groups
Manufacturing Design
In new product development, the key to differentiation is to develop both the product and production technology at the same time. Fujikura possesses advanced equipment development technologies, including mechanical design and electrical/control design, and develops unique equipment that does not exist anywhere else in the world. We continue to deepen our in-house equipment technologies that we have cultivated thus far and to master the use of cutting-edge equipment technologies available in the world, incorporating these technologies into original production equipment tailored to our products while challenging ourselves to develop cutting-edge equipment. By providing production equipment and production technologies, we are working to increase the profitability of each business units and R&D unit and develop competitive new products.
Furthermore, in order to cope with the recent decline in the working population, there is a demand for further automation of manufacturing processes.We aim to provide production technology that can simultaneously improve productivity, stabilize quality, and reduce manpower by replacing tasks that were previously performed by hand with dedicated machines, robots, and automatic transport machines.
Precision Machining Technology
In the field of manufacturing products that are becoming more and more precision, precision machined parts, jigs, and molds are used to minimize process variability and achieve high productivity and high yields.
By making full use of high-precision cutting, grinding, electrical discharge machining, and measurement technologies, we have achieved product differentiation and increased competitiveness by in-house production and black box of high-precision jigs that are indispensable for Fujikura's Optical Fiber manufacturing. In addition, various molds such as molding, punching, and sequential feeding are manufactured in Fujikura Group to improve product accuracy.
The precision machining technology is application in the product manufacturing, and the company manufactures its own in-house cutting blades and uses them to manufacturing tens of millions of electronic components annually with high processing capacity.
In the R&D field, we are developing precision machining methods for difficult-to-cut materials such as heat-resistant alloys and rare metals, as well as new materials, by making full use of various high-precision processing machines, including high-speed machining machines that can process with an accuracy of 1/1000 mm or less.
By developing precision machining technology, we aim to realize differentiated products and manufacturing by providing precision jigs, parts, and processing methods.
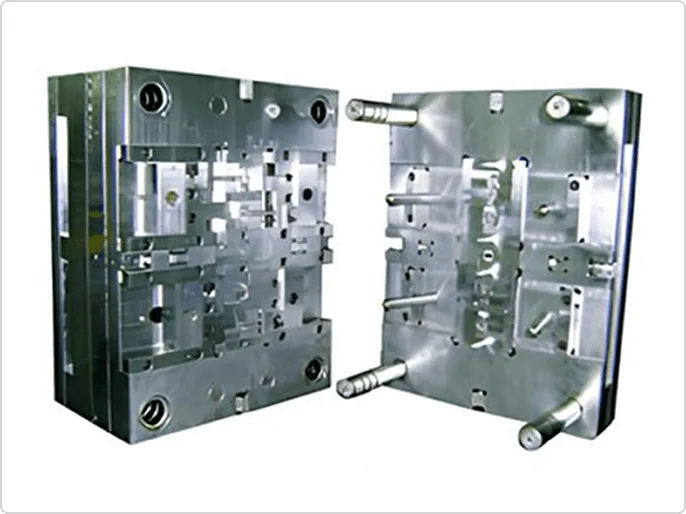
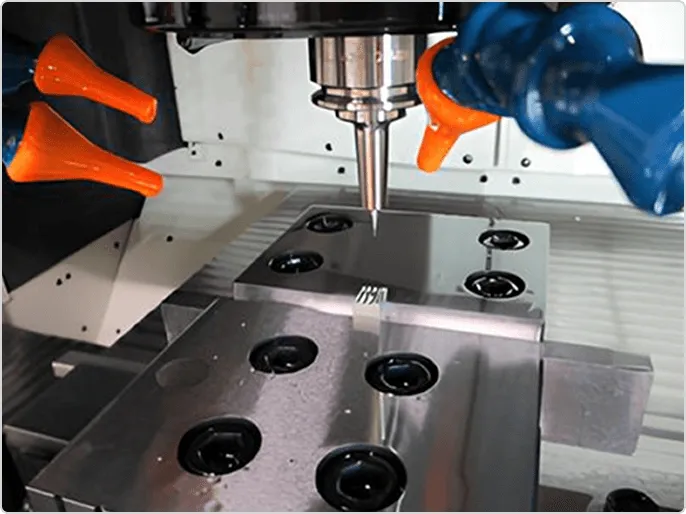
Control Technology
The Production Technology unit utilizes advanced control technology to develop in-house manufacturing equipment. manufacturing equipment requires advanced and high-precision products, stable quality, labor savings, and most importantly, work safety. We actively incorporate advanced control technologies such as high-speed and high-precision speed control and positioning control, and we are also building control systems for robots and unmanned transport vehicles to reduce the number of workers in factories and make them unmanned. In addition, in order to acquire digital data from manufacturing equipment (FA layer), we are closely involved with the Monodukuri site, acquiring useful data through optimal sensing, and utilizing the acquired data to add value to the data, thereby promoting "Monodukuri DX" and working to make manufacturing equipment more intelligent.
Inspection Technology
Products in the information and communications and energy fields require stable, high quality to support a stable social infrastructure. In the electronics and automotive fields, as products become more sophisticated and denser, it is necessary to accurately detect minute defect and changes in quality and prevent the outflow defect products. All products require quality control (QC) through rigorous and strict inspection and continuous quality improvement, and it is necessary to develop optimal inspection methods tailored to strong point / feature of each product.
In our production technology unit, we work with each related unit, such as product development, manufacturing site, quality assurance (QA), and inspection technology, to develop unique inspection methods that are tailored to strong point / feature, manufacturing process, and inspection standards of each product. We have introduced highly sensitive and highly accurate inspection equipment into many manufacturing processes for a wide range of products within the company. In addition to inspection, we also develop and introduce production systems that visualize quality trends and changes from inspection results, leading to quality improvements.
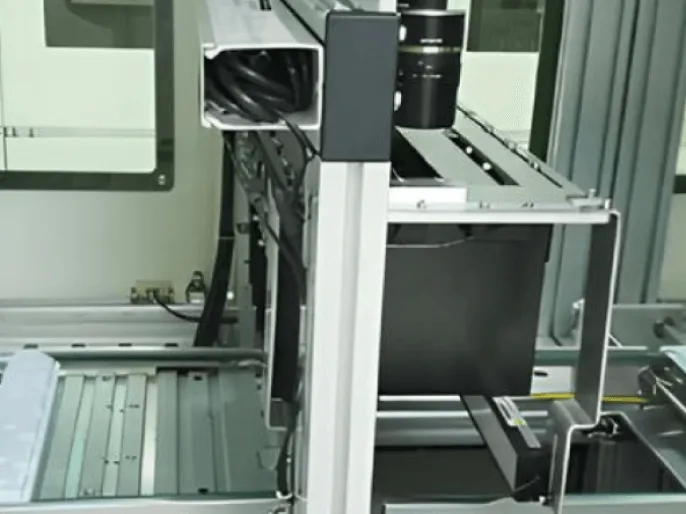
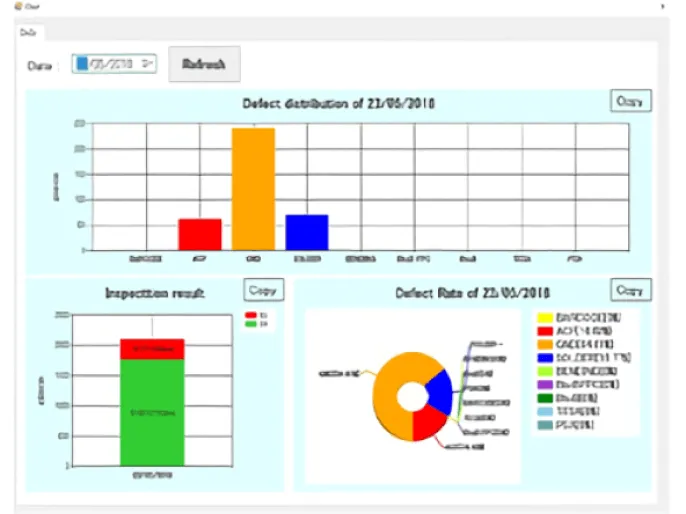
Material Analysis Technology
By utilizing MI (materials informatics) in material technology, Fujikura is strengthening its Monodukuri and contributing to society. MI is an approach that actively utilizes computational science and data science. Material technology involves elements such as material design, process design, and measurement and analysis, so it is necessary to use appropriate data analysis methods for these. Fujikura positions MI as one of its fundamental material technologies and is working to apply it to a wide variety of products. For example, by utilizing Bayesian optimization in the development of cable sheaths, we have succeeded in shortening the development period to about one-quarter of the conventional time.
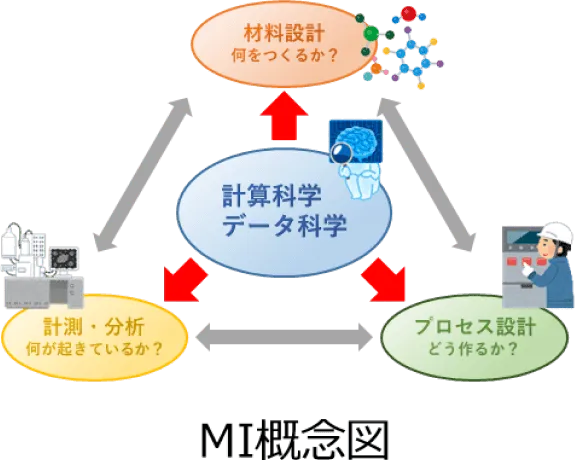
Analysis Technology
Computer simulation* analysis, which is increasingly being used in product development, manufacturing and processing technology development, and investigation of the causes of defects, makes it possible to "visualize" and "understand and examine" invisible phenomena and changes that can only be imagined, and is a very useful method for obtaining optimal solutions for product design and shortening product development times. Computer simulations used in the design and improvement of manufacturing processes are analyses that combine multiple physical phenomena, such as simultaneous coupled analysis of fluid behavior and chemical reactions of raw materials, and understanding of changes in shape and stress distribution due to vibration, and the technical challenge is how to ensure analytical accuracy for such complex phenomena. By feeding back actual manufacturing data to computer simulations, we accumulate our own analytical techniques and know-how to improve analytical accuracy, and we make full use of various analytical techniques such as stress, displacement, vibration, strength, fluid, heat transfer, and electric current to develop differentiated products and production technologies.
Computer simulation: Using a computer to simulate phenomena or events that are difficult to calculate by hand.
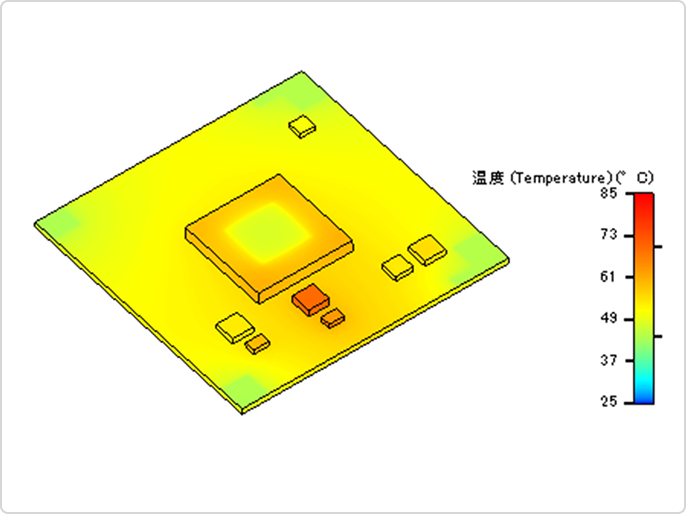
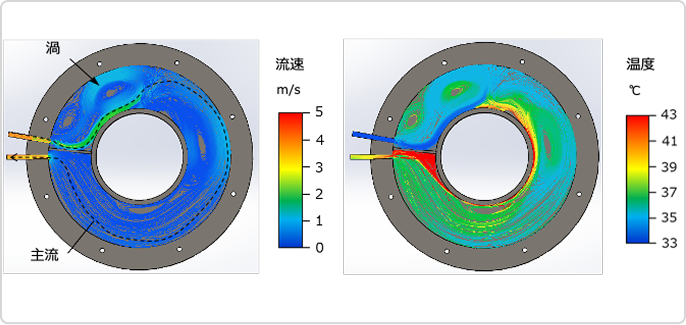
AI technology
In recent years, with the rapid spread of AI technology, an increasing number of manufacturing companies are introducing AI into their production processes. Fujikura is working to dramatically improve quality and productivity by introducing its own AI technology into its in-house manufacturing processes.
We believe that one of Fujikura's AI technology competencies is the ability to acquire the latest AI and application it to solve actual business problems as a solution. Specifically, in 2018, we introduced a visual inspection application to the manufacturing process, and since then, we have developed and implemented multiple AI-based visual inspection systems for a wide range of products within the company. In addition, Fujikura's own "AI platform" is also being developed to monitor the normal operation of the developed AI solution and to maintain stable AI inspection operation.
Discrimination AI is one of Fujikura's key technologies, and the concept behind it is shown in Figure 1. During learning, a large number of pairs of images and their corresponding accurate information are input into the network. As learning progresses, it becomes possible to output results for input images with high accuracy. Fujikura uses this technology for visual inspection in manufacturing process.

Figure 1. Image recognition using deep neural networks
We are also working on developing applications using reinforcement learning and Sim2Real technology. These technologies have the potential to expand the scope of AI application, as aspect determined by AI can be used to control manufacturing equipment. Fujikura has conducted proof of concept testing to introduce this technology into a lens alignment system [2][3].
Going forward, we will continue to keep up with the ever-advancing AI technology and promote the use of AI to address issues that arise in our Monodukuri and business operations, thereby improving work efficiency and productivity.
References
- Kurosawa et al., "Methods for promoting AI and technological development to realize it," Fujikura Technical Report, 2021.
- T. Akiyama, "Practical Use Case of Reinforcement Learning and Sim-to-Real Transfer for Manufacturing", NVIDIA GTC 2023.
- Nitawaki et al., "application of AI control technology using reinforcement learning and Sim2Real to manufacturing equipment," Fujikura Technical Review, 2024.