- HOME
- Products
- Fiber Laser
- Diverse processing solutions
Diverse processing solutions
Fiber laser processing video
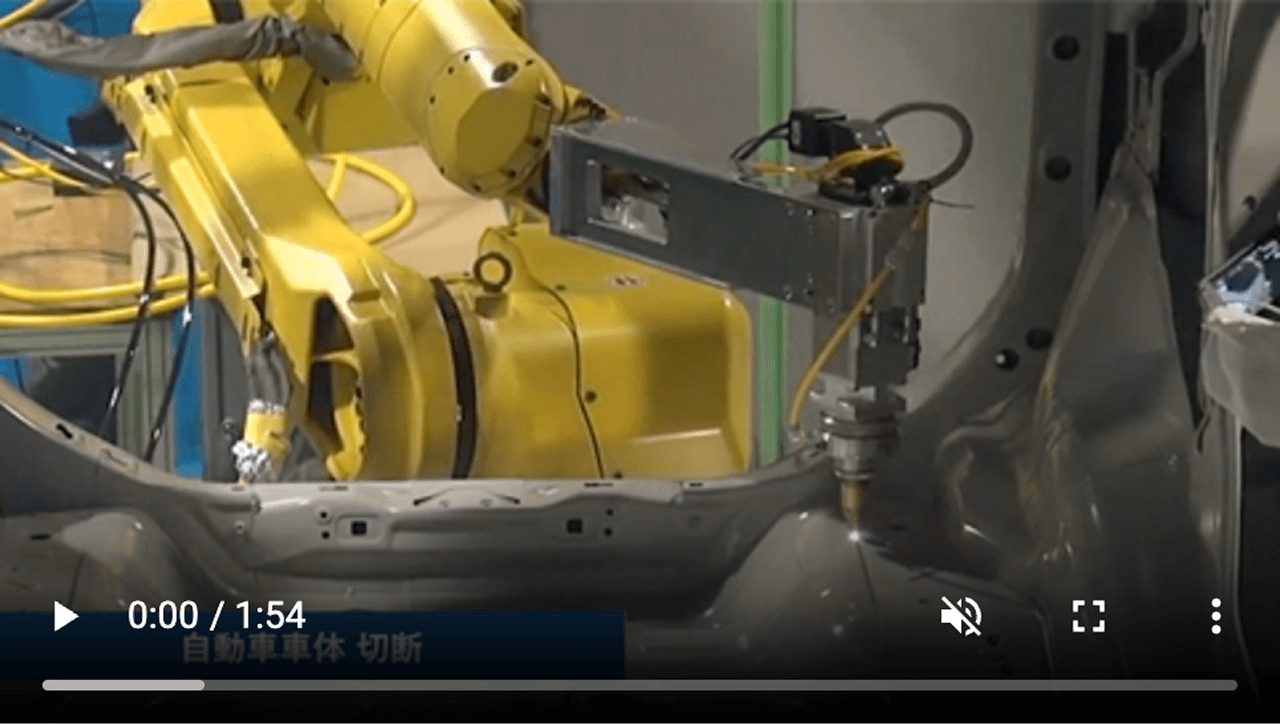
Fiber Laser Cutting
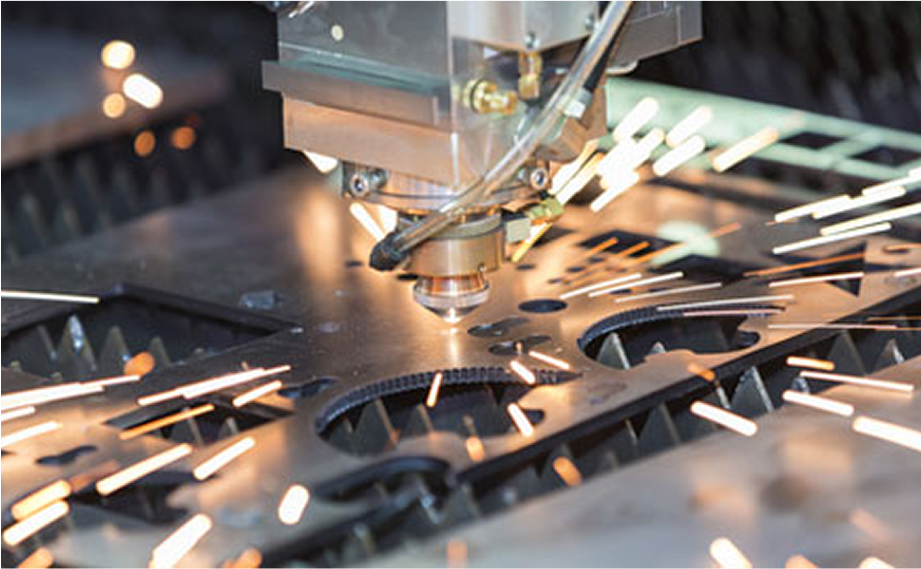
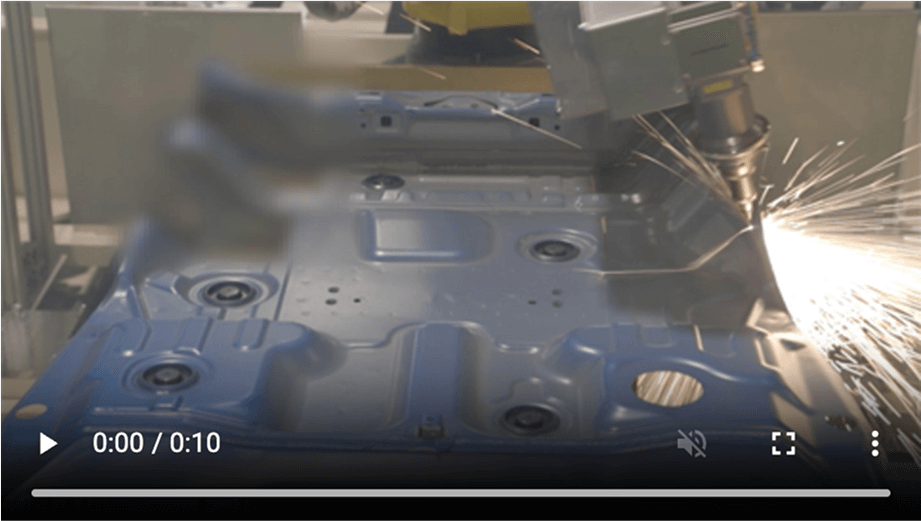
Achieves high energy density
Thick metal plates can also be processed with high precision.
Fiber lasers are used to process a wide range of materials, from metals to plastics.
The excellent beam quality allows the spot size to be narrowed, enabling high-precision cutting with high energy density.In addition, by realizing a high-output laser in the kW class, it is possible to cut not only thin plates but also thick plates with high precision, meeting the various cutting needs of our customers.
Relationship between cutting speed and plate thickness (power: 500 W - 6 kW)
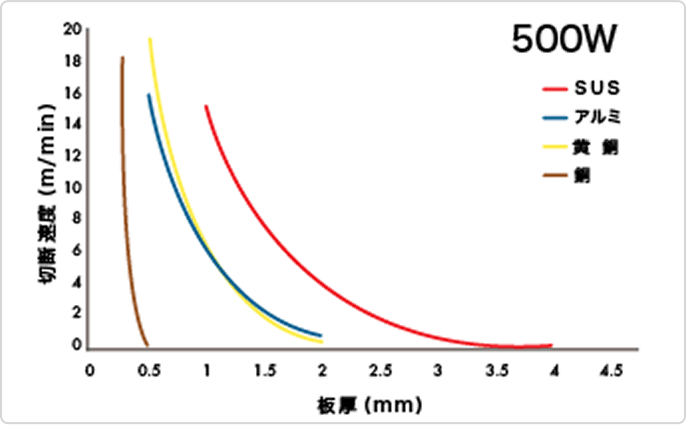
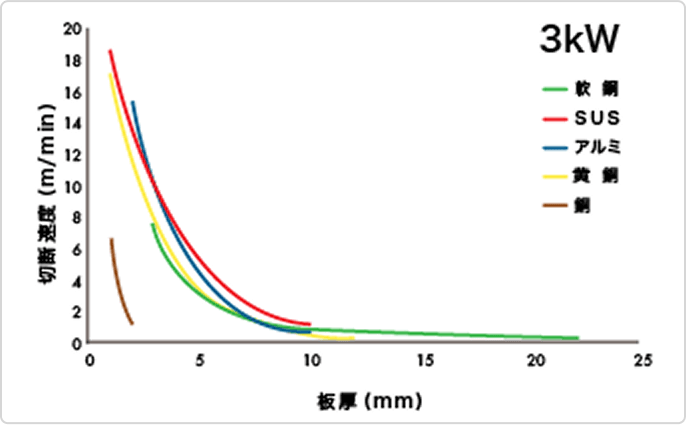
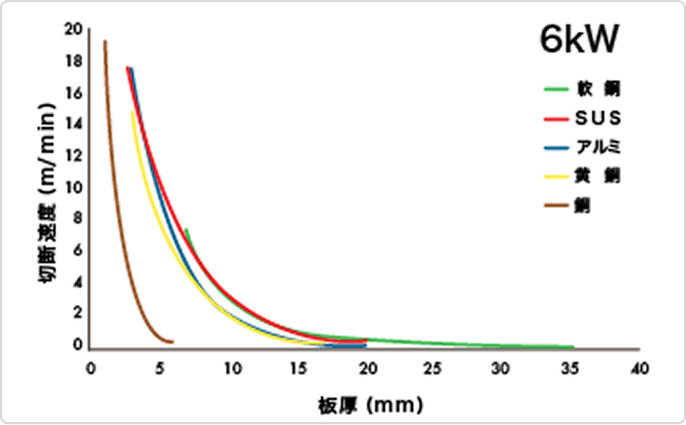
output | SS400 (mild steel) | SUS | aluminum | brass | copper |
---|---|---|---|---|---|
500W | - | 4 mm | 2 mm | 2 mm | 0.5 mm |
3 kW | 22 mm | 10 mm | 10 mm | 12 mm | 2 mm |
6 kW | 35 mm | 20mm | 20mm | 17 mm | 6 mm |
- The values in the table indicate the maximum plate thickness that can be cut when using a Fujikura oscillator.
- There is no reflected light error even when processing highly reflective materials.
- This processing data does not guarantee processing.
- Processing performance may be improved by optimizing the laser oscillation conditions and peripheral optical systems and equipment.
Fiber Laser Welding
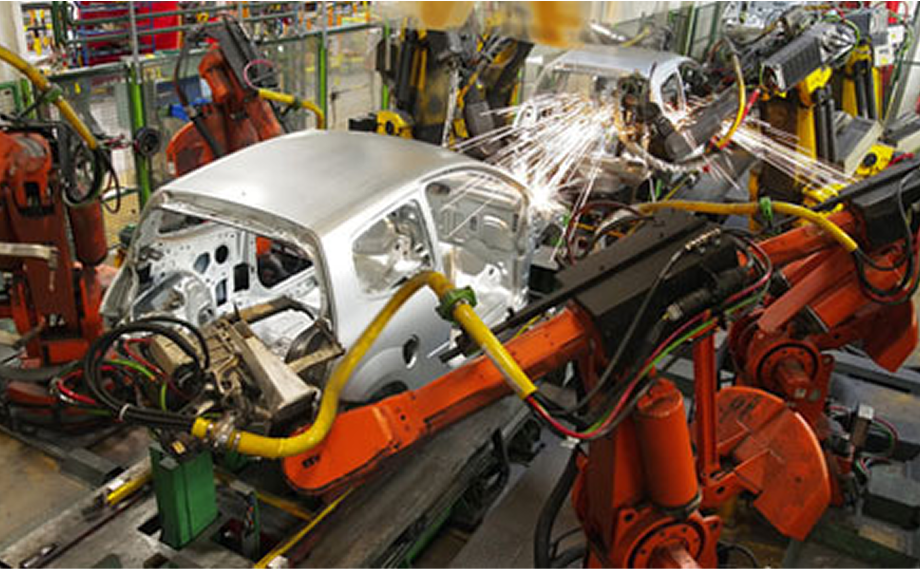
An outstanding product that overturns conventional wisdom
Providing welding quality
Fiber lasers will overturn conventional wisdom about welding.
Smooth welding is possible due to the continuous oscillation of the laser. In addition, the excellent beam quality allows for a high-brightness beam to be emitted with a small focal size, which reduces distortion of the material. Fiber lasers provide unprecedented high welding quality. Since a single machine can perform various types of welding, the number of welding processes can be reduced, and the high output strong point / feature allows for a dramatic increase in welding speed, greatly improving productivity. In terms of cost, fiber lasers have a higher electrical conversion efficiency than conventional lasers and do not require maintenance, which allows for a significant reduction in running costs.
Relationship between welding speed and penetration depth (power: 500W - 6kW)
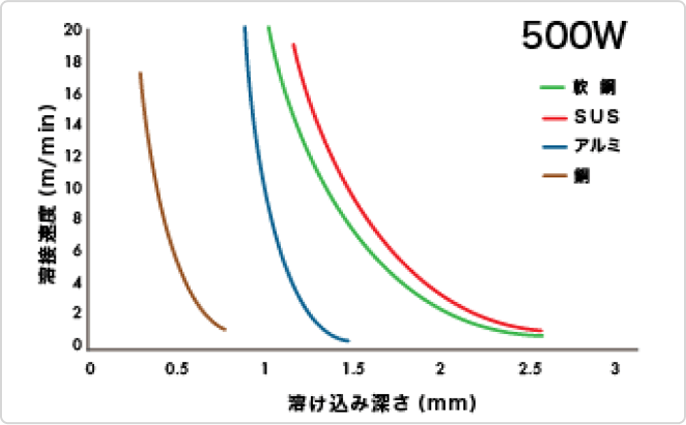
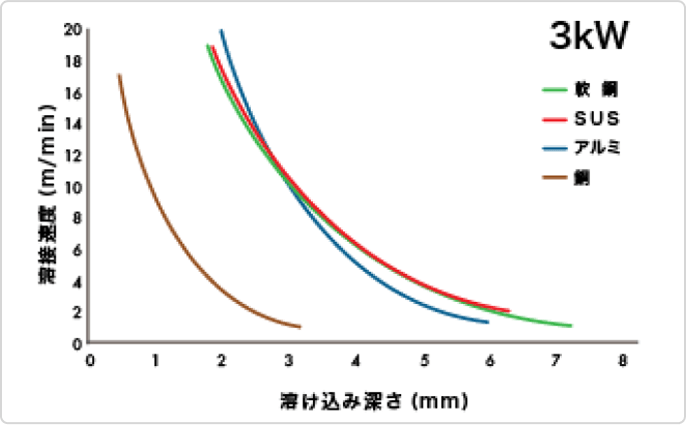
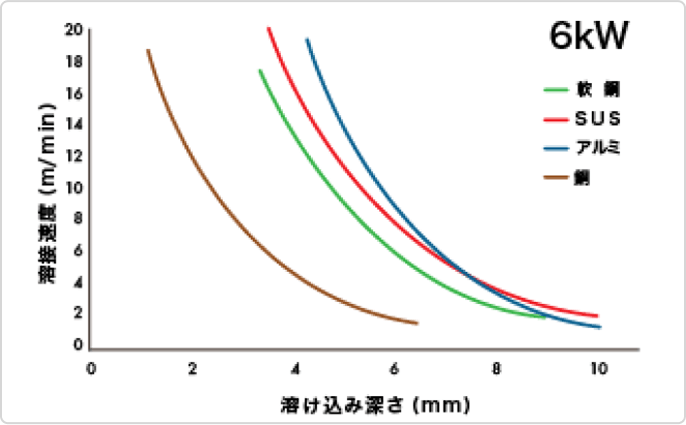
output | SS400 (mild steel) | SUS | aluminum | copper |
---|---|---|---|---|
500W | 2.6 mm | 2.6 mm | 1.5 mm | 0.8 mm |
3 kW | 7 mm | 6 mm | 6 mm | 3 mm |
6 kW | 9 mm | 10 mm | 10 mm | 6 mm |
- The values in the table indicate the maximum plate thickness that can be welded when using a Fujikura oscillator.
- There is no reflected light error even when processing highly reflective materials.
- This processing data does not guarantee processing.
- Processing performance may be improved by optimizing the laser oscillation conditions and peripheral optical systems and equipment.
Fiber laser plastic welding
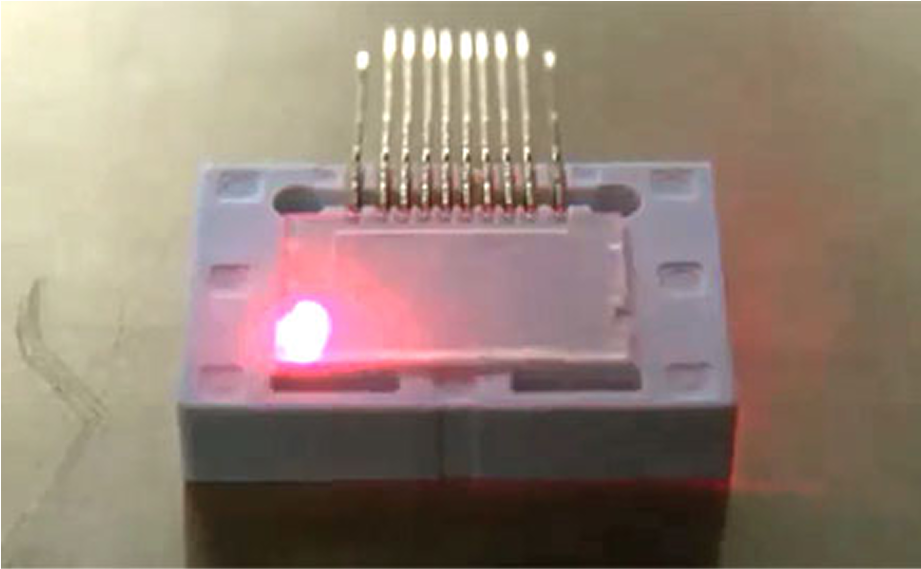
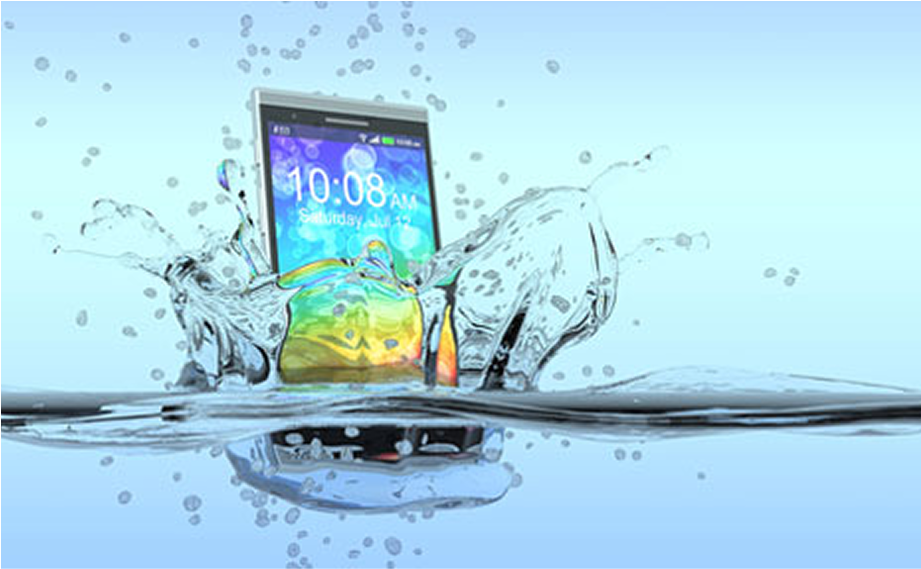
Contributing to waterproofing electronic devices and reducing the weight of automobiles
Laser plastic welding is a processing method in which a laser beam is irradiated onto the target material, generating heat at the boundary between the materials, and welding the materials together. Laser plastic welding uses a combination of a transmitting material that transmits the laser beam and a absorbing material that absorbs the laser beam.
It enables high speed, airtight joining and even welding that was difficult using existing processing methods.
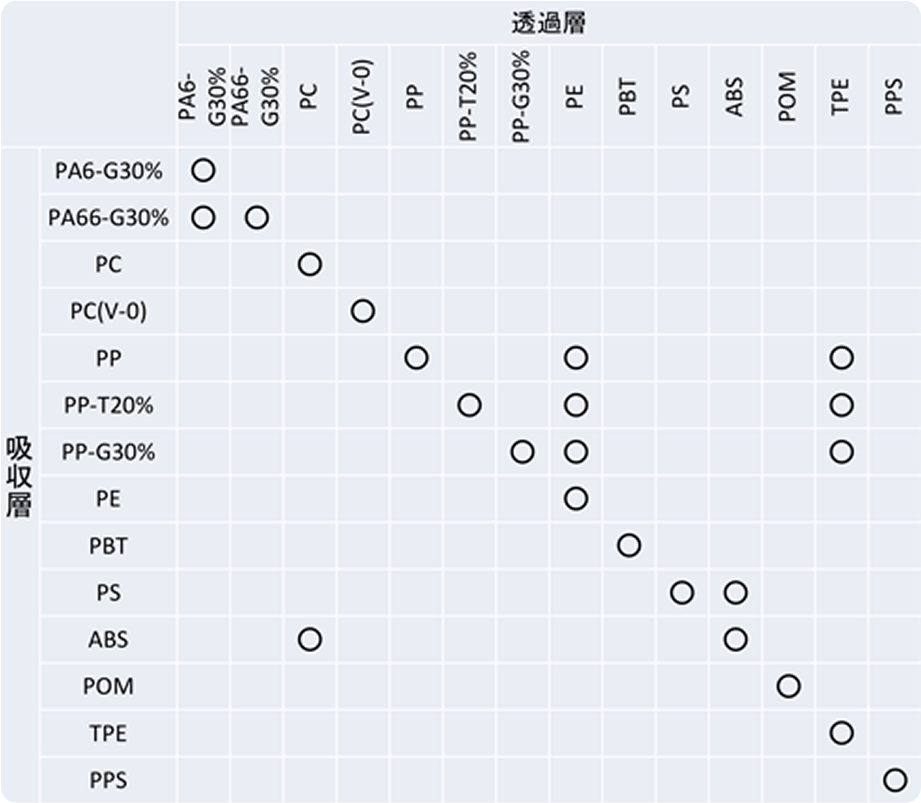
Relationship between welding speed and penetration depth (power: 500W - 6kW)
Laser cleaning
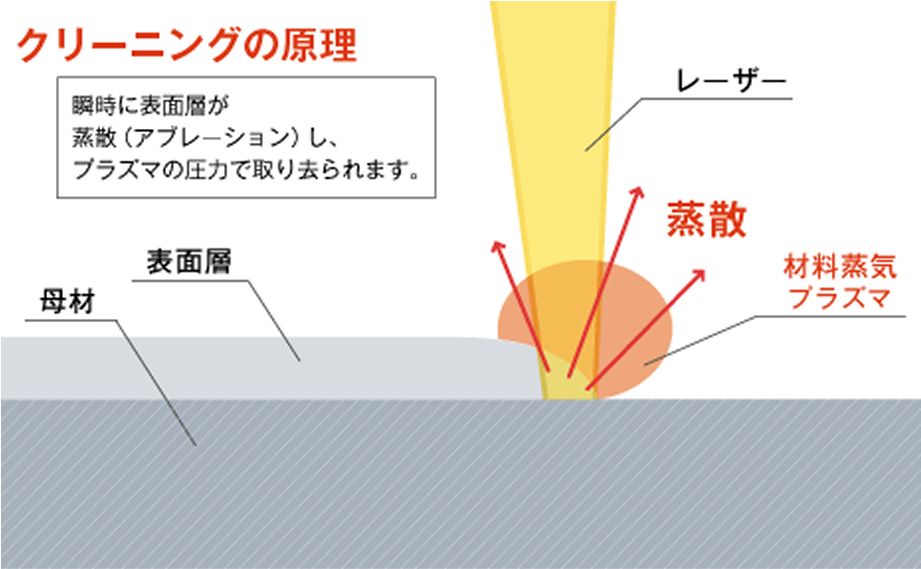
Our high peak power
Pulsed fiber laser
Realizing high-definition and precise cleaning processing
Laser cleaning is a dry environment cleaning process that does not use solvents or water, does not require the treatment of secondary disposal materials, and unlike mechanical cutting, is a non-contact process, making it possible to clean without damaging the base material itself. It is beginning to be used in a wide application range of applications, including removal of paint and oxide layers prior to welding, rust removal from molds and component surfaces, cleaning and finishing processes, and removal of paint films and plating layers.
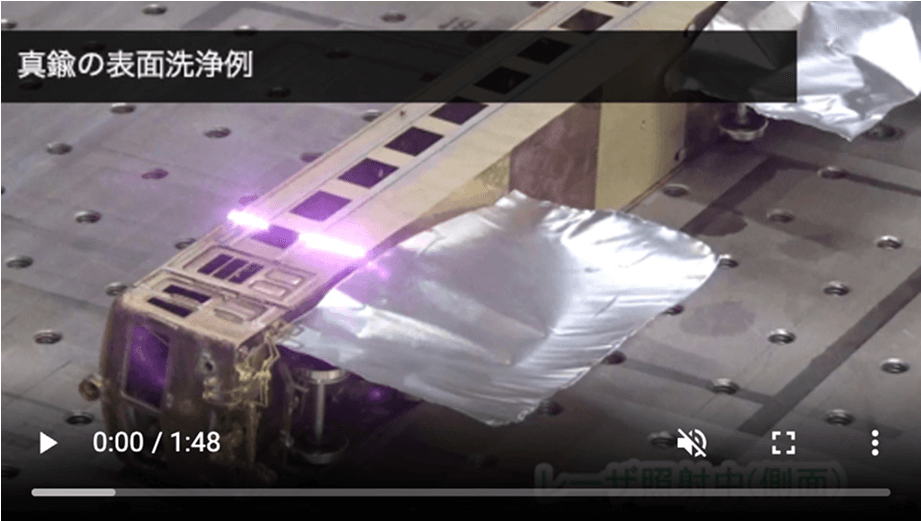
Provided by: IHI Inspection & Instrumentation Co., Ltd.
Brass surface cleaning example
Here is an example of surface cleaning of a brass model train. Normally, one would try to remove rust and fingerprints using a neutral detergent or cleanser, as well as cleaning products such as brushes and scrubbing pads, but it is not easy to remove dirt from finely molded areas. Surface cleaning using laser cleaning allows for uniform cleaning without scratching the finely molded areas. In the video, the laser irradiated and non-irradiated areas are distinguished and compared. As in the video of paint peeling from the bolt area, even the smallest uneven areas were quickly cleaned.
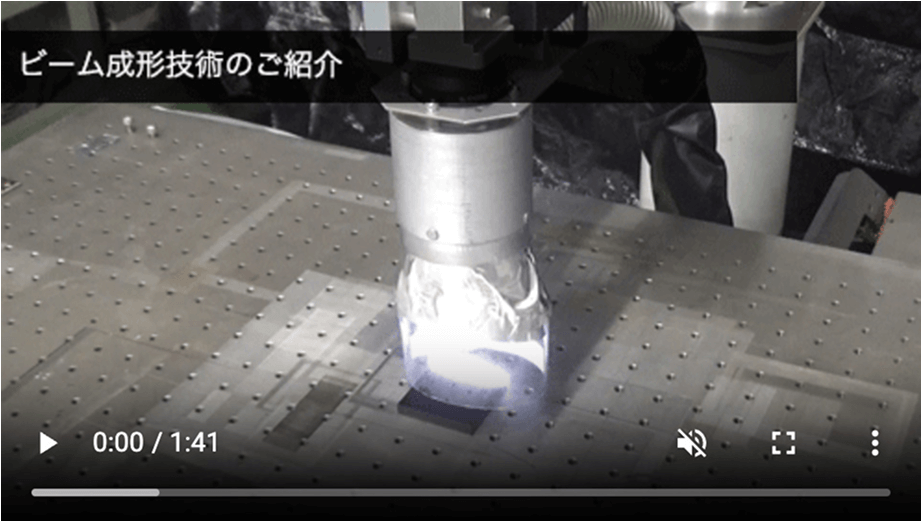
Provided by: IHI Inspection & Instrumentation Co., Ltd.
Introducing Beam Shaping Technology
One of the challenges with laser cleaning is that, depending on the material, scratches or irradiation marks may remain on the base material. Particularly under conditions of high average laser power, minute irregularities are likely to form on the surface of the base material, which will remain as irradiation marks.
This problem can be solved by shaping the beam to suit the desired processing. In this article, we will introduce a method that incorporates a special optical system into the irradiation head and does not damage the mirror surface.
In the video, we compared the state of the base material after irradiation with and without the special optical system. Without the special optical system, the base material was irradiated with the laser and changed from its mirror state, but when the laser was irradiated through the special optical system, the base material was not affected and the mirror surface of the base material was preserved even after the black layer on the surface was removed.
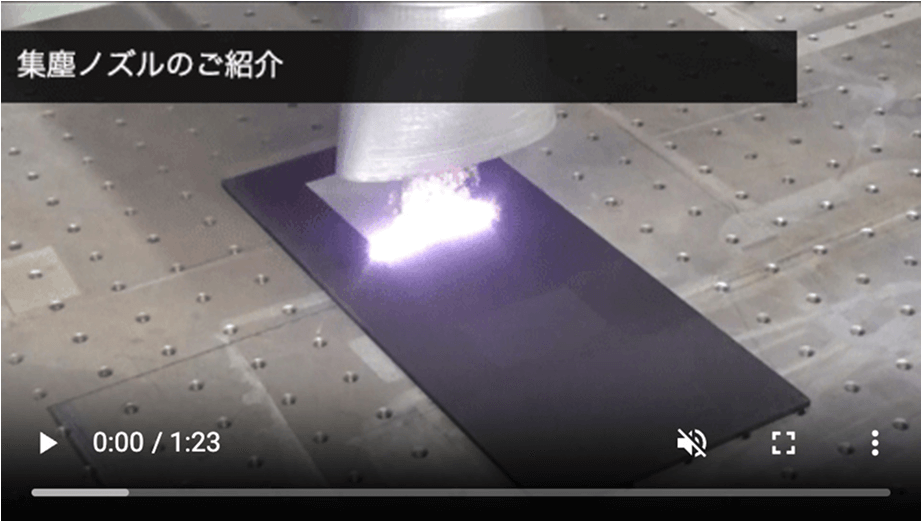
Provided by: IHI Inspection & Instrumentation Co., Ltd.
Introduction of dust collection nozzles
Laser cleaning can remove rust and paint, but depending on the material, it can generate a lot of dust. Large amounts of dust can have adverse effects on the human body. In addition, dust that adheres to the laser output port can reduce the removal ability and cause damage to the protective glass.
Conventionally, dust was collected by placing suction or exhaust equipment (dust collectors) near the irradiated material, but the generated dust scattered and was difficult to collect, resulting in issues with the dust scattering and remaining on the target material and its surroundings.
To address this issue, the dust collection nozzle introduced here makes it possible to collect dust without scattering it. This dust collection nozzle has a unique design that prevents the collected dust from adhering to the laser output port, so there is no decrease in removal capacity. It can also be attached to existing irradiation heads. Using the dust collection nozzle can solve the issue of dust processing and reduce running costs.
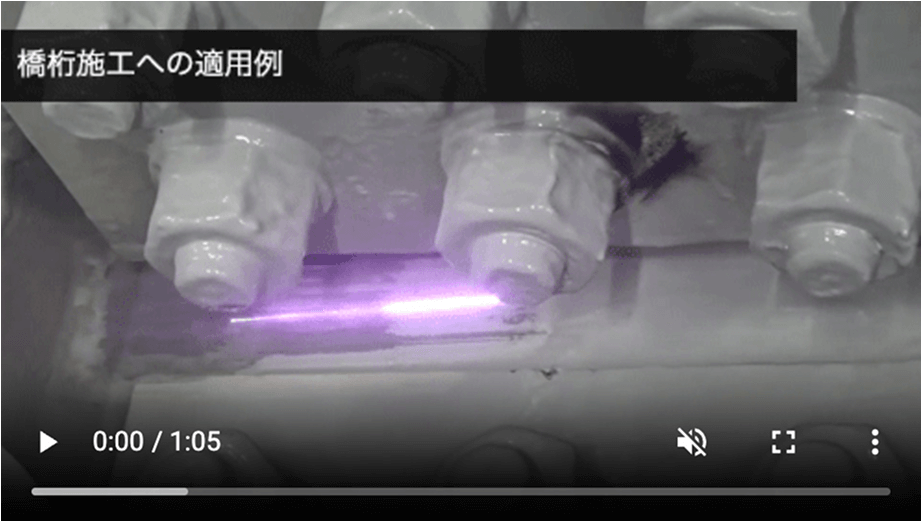
Provided by: IHI Inspection & Instrumentation Co., Ltd.
application example for bridge girder construction
Bridges are exposed to the elements for decades, causing the paint to deteriorate and rust to appear. Therefore, work is periodically carried out to remove the old paint, scrape off the rust, and repaint the bridges.
However, the bolted and welded areas are so intricate that the tools needed to remove the paint cannot reach them. Because these areas are important for maintaining the strength of the bridge, there is a need for improved construction methods that can ensure reliable work.
Laser cleaning has the ability to meet these expectations. Even in narrow gaps, as long as light can pass through, it is possible to remove paint and rust. In this video, we will show you how to remove the corners of a three-sided weld. You can see how the laser can be used to remove paint and rust without any problems, even in the deepest places.
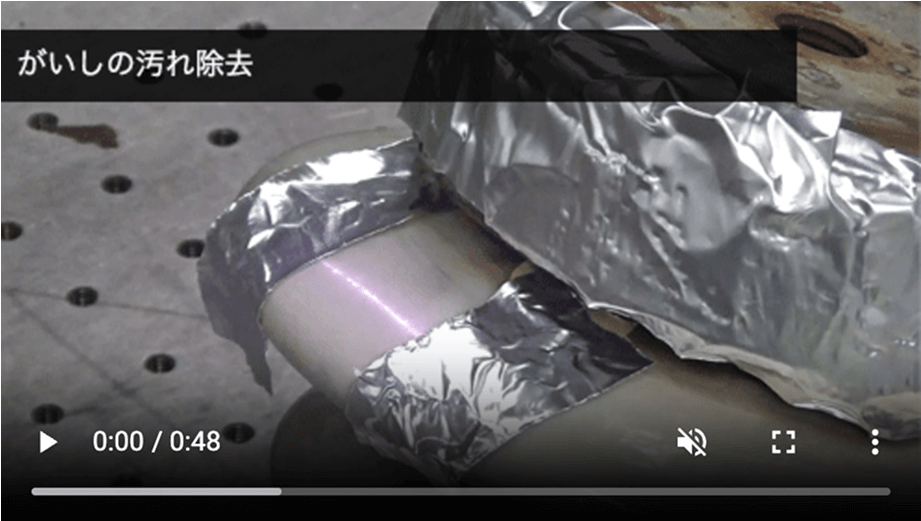
Provided by: IHI Inspection & Instrumentation Co., Ltd.
Surface cleaning that suppresses irradiation marks
(Removing dirt from insulators)
Insulators are made of materials such as glass, porcelain, and synthetic resin, and are used on utility poles, steel towers, trains, etc. to provide electrical insulation for electric wires. When insulators are used for a long period of time, dirt accumulates on their surfaces, increasing the risk of creeping discharge. Therefore, to prevent accidents, regular cleaning of insulators is required. By adjusting the laser irradiation power and irradiating multiple times, laser cleaning can remove dirt without leaving any marks on the insulator surface. In addition, because laser cleaning is non-contact and dry cleaning, it is easy to control remotely and is also effective in protecting the environment.
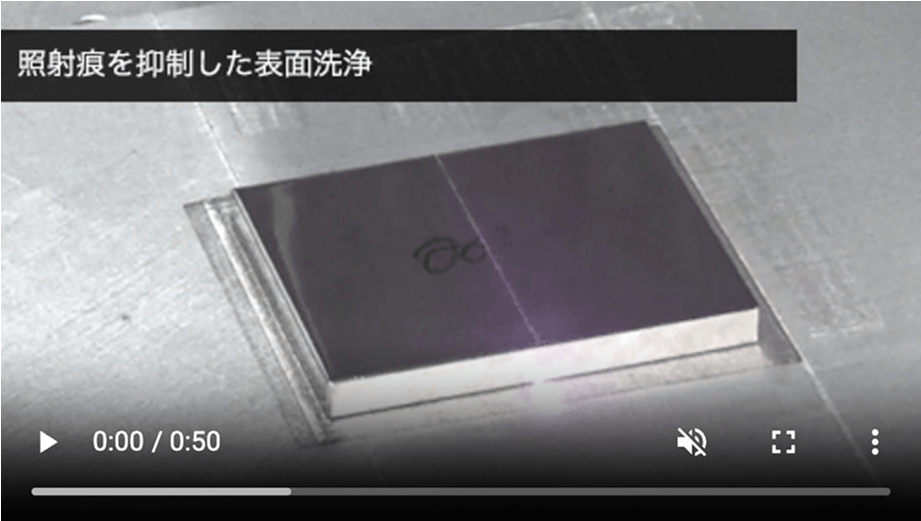
Provided by: IHI Inspection & Instrumentation Co., Ltd.
Surface cleaning that suppresses irradiation marks (removal of oil-based markings on the surface of SUS-based materials)
When dirt adheres to the surface of a material and is to be removed, there is usually a possibility that the surface of the material may be scratched. With laser cleaning, by adjusting the laser irradiation power, dirt can be cleaned without leaving irradiation marks on the metal surface.
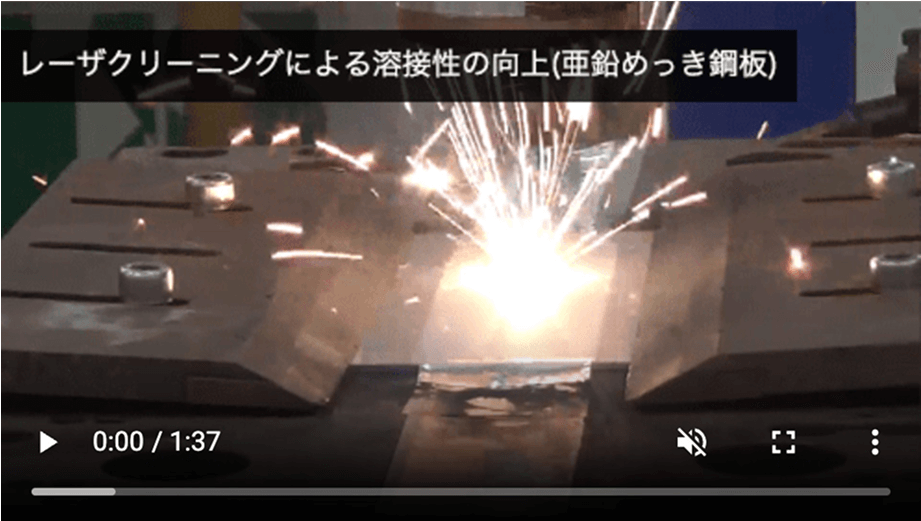
Provided by: IHI Inspection & Instrumentation Co., Ltd.
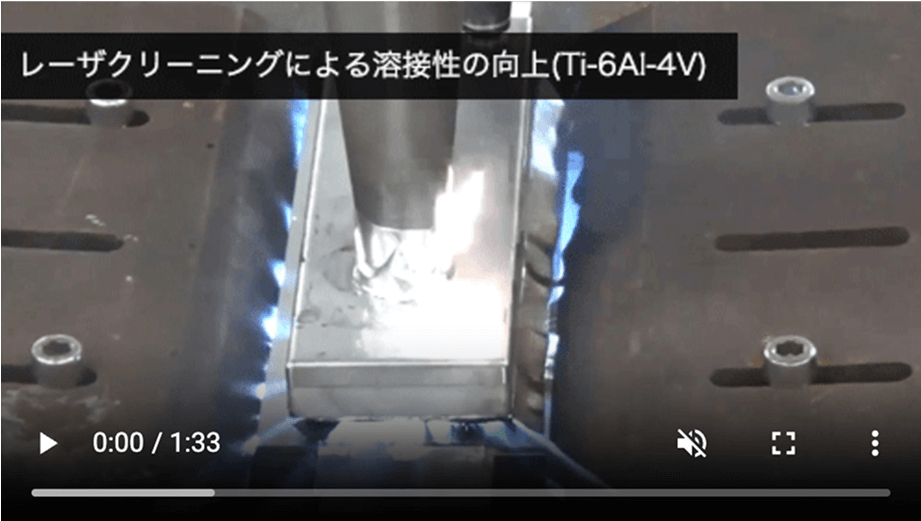
Provided by: IHI Inspection & Instrumentation Co., Ltd.
Improved weldability through laser cleaning (galvanized steel sheet, 64 titanium
(Ti-6Al-4V)
In welding, reducing internal defects after welding contributes to improving the quality of the weld. Cleaning the material surface before welding is effective in reducing internal defects.
For zinc-plated steel sheets, which have excellent rust resistance and are used for automobile bodies, we compared weldability with and without the removal of the plating layer before welding. As a result, we were able to confirm that removing the plating layer with a laser reduced internal defects after welding.
In laser welding of galvanized steel sheets, there is a method to reduce internal defects by leaving a space (gap) between the sheets, but by cleaning with a laser, gap management and wire addition can be eliminated.
For 64 titanium (Ti-6Al-4V), which has traditionally been considered difficult to weld, we compared weldability by cleaning the butt surfaces of the material. As a result, we found that laser cleaning was superior in reducing internal defects compared to acetone cleaning and applying a rust inhibitor.
In either case, application laser cleaning as pre-welding treatment enables welding with extremely few internal defects.
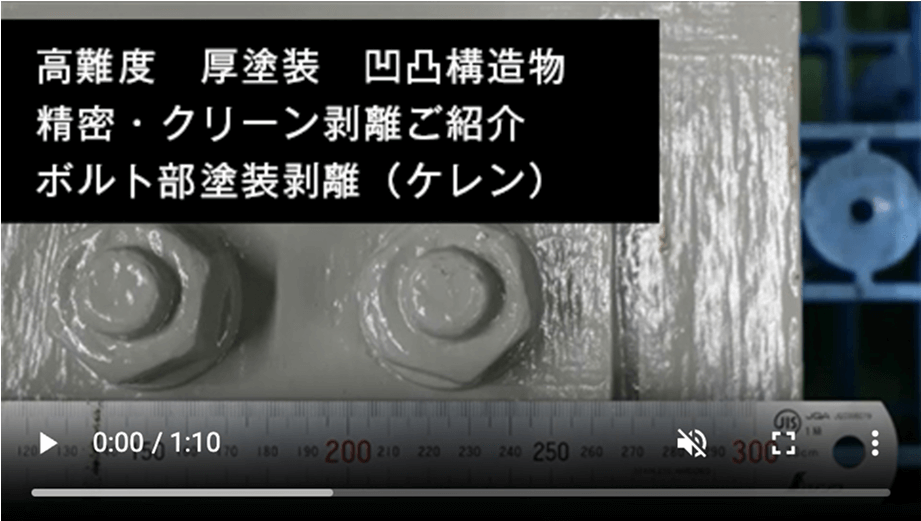
Provided by: IHI Inspection & Instrumentation Co., Ltd.
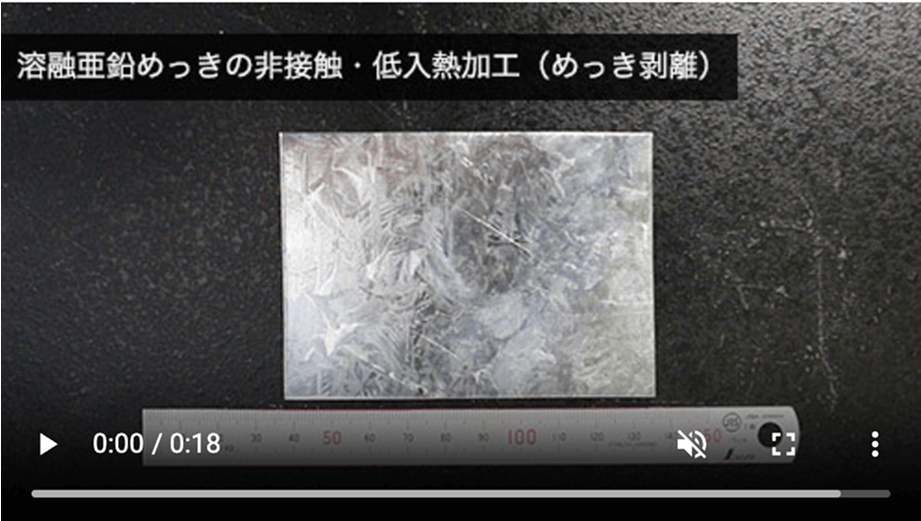
Provided by: IHI Inspection & Instrumentation Co., Ltd.
High beam quality laser enables stable, high quality processing even when done manually
There are various methods for removing paint, but power tools can be noisy. Blasting requires care as the blasting material scatters. Chemical removal is problematic because it is difficult to application to bolts and there have been many accidents. Using lasers solves these problems.
Furthermore, our lasers have a long Rayleigh length due to their high beam quality, which ensures stable processing quality. In addition, the small spot diameter enables precise irradiation even on uneven surfaces in minute areas such as bolts. In addition, non-contact processing with high peak power enables high-quality processing that removes only the paint film without damaging the coated object.
Power tools | Blast | Medicines | laser | |
---|---|---|---|---|
Work time | △ | △ | 〇(short) | △ |
Drug process |
× | 〇(Not required) | ||
In process noise |
× | 〇(none) | ||
In process Flying debris |
× | 〇(very small) | ||
quality Stability |
〇 |
Product finder
- HOME
- Products
- Fiber Laser
- Diverse processing solutions